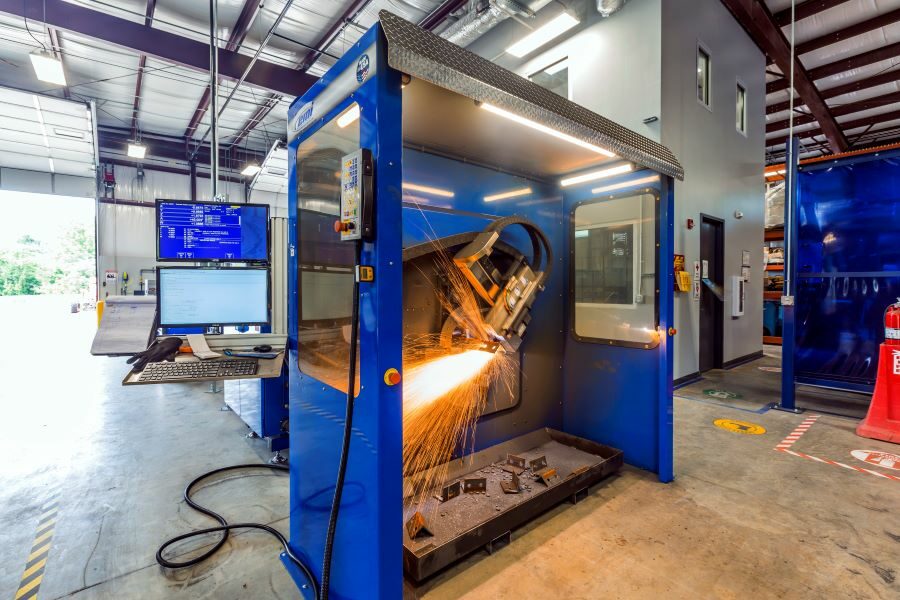
Turner Launches xPL Offsite, an In-House Manufacturing and Assembly Company
Turner Construction Co. on May 6 launched xPL Offsite, a wholly owned subsidiary that leverages design for manufacturing and assembly (DfMA) techniques to develop construction products and enable projects to be delivered via offsite manufacturing (OSM) capabilities.
xPL Offsite draws from Turner’s more than 20 years of real-world application in offsite manufacturing, prefabrication and modular construction, according to the company. Turner has completed 500 projects valued from $100 million to more than $1 billion.
Turner’s Hyperscale Data Center Program extensively used DFMA capabilities led by executives now leading xPL Offsite. Their past efforts include delivering 13 standardized, prefabricated products to 23 data center campuses across the U.S. The products fabricated include conveyance modules, electrical skids and pump houses. xPL is managing four vendors and collaborating with several general contractors on this $400-million program to standardize costs while improving consistency and quality in the field.
ENR previously reported about the prefabrication methods used on San Francisco International Airport’s Terminal 3 Expansion. Turner is part of a design-build team that built prefabricated modules to create temporary passenger corridors as part of a $2.6-billion project. A 1,000-ft West Corridor and a 400-ft East Corridor were fabricated as 11 modules at an air cargo yard and transported across the airfield overnight, which accelerated the project schedule.
For Panasonic’s Energy Electric Vehicle Battery Manufacturing Plant, xPL Offsite integrated a 2,200-linear-ft structural steel conveyance, incorporating all piping and electrical utilities, for a 5.5-million-sq-ft lithium-ion battery assembly factory in De Soto, Kan. The application of DfMA provided a safer working environment, integrated fabrication and improved productivity by moving the trade partners’ work to a dedicated environment. The offsite construction of major components addressed labor availability challenges and completed scopes of work that were in the project’s critical path in a controlled setting that overcame site and schedule constraints.
“Customers are asking us for accelerated deliveries. They’re asking us to build in more remote locations. They’re asking us to build mega projects that require a significant amount of labor, a significant experience and there are significant complexities to these projects,” says Drew Kerr, a Turner vice president and general manager of the new xPL Offsite division. “They’re asking us to figure out how to do this.”
Part of Turner’s investment in xPL Offisite is an expansion of an existing fabrication facility in DeCatur, Ala., with equipment such as Lincoln Python technology for steel material reduction; ABB robotics for precision beam assembly and FabStation for optimized fabrication processes.
“Our previous manufacturing facility was only in the 15,000- to 20,000-sq-ft range. There was only so much capacity,” Kerr says. “With this expansion, this launch of xPL offsite, we made an investment to expand… procure and invest in some additional equipment to support a higher capacity and a higher opportunity.”
Kerr said xPL Offsite’s services will include tailored planning; integrated expertise combining prefabrication, manufacturing management and Turner’s project management capabilities for complex projects and environments; products that are versatile, customizable kits of parts covering major construction disciplines, including central utility plants; MEP skids and racks; modular bathroom pods, clean rooms and IT closets.
Post a Comment
You must be logged in to post a comment.