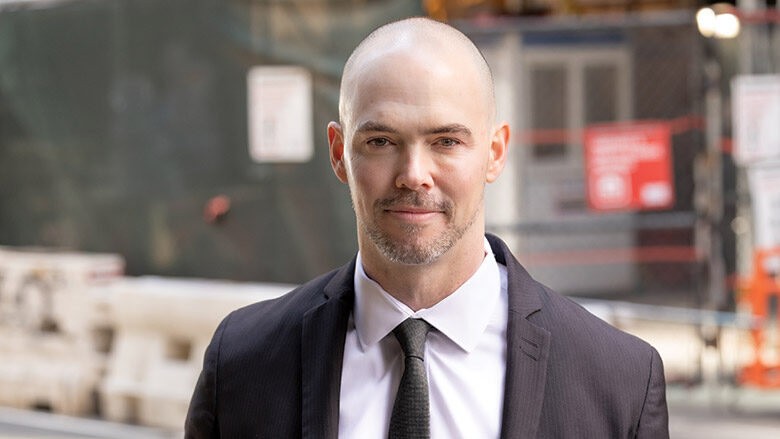
Steve Burke: Leader in Sustainable Construction
Steve Burke
39, Senior Director, Sustainability
Suffolk
Boston
As a sustainability professional who has worked on both project design and construction at Boston-based construction management firm Suffolk, Burke easily moves from one to the other and interacts well with peer professionals on both sides.
“When we’re actually reviewing the design and reviewing the drawings, we can come back to an owner and give them the list of recommendations that look at the lifecycle of a property and investment,” he says, “The systems that are going to help you achieve the best energy performance and lowest operating cost, but also the lowest lifetime cost with the maximum amount of benefit and value. On top of that, you get environmental attributes layered in.”
Burke, who has given more than 50 external presentations on sustainability, cochairs the Carbon Leadership Forum of Boston, a partnership with the Boston Society of Architects.
He says knowing how to convince owners on the business case for building sustainability by focusing on issues such as energy independence and security is particularly important at a firm with clients in different areas of the country and with different political views.
Clients building in “highly vulnerable” markets “completely understand what those issues are,” Burke says.
“One of the biggest potential shortcomings in the sustainability space is that we try to lead by virtue, instead of by the business piece of it. The consequences of our actions and the larger considerations of the environmental impacts of what we’re doing, is important. That’s why the sustainability professionals are in the careers that they’re in,” he insists. “But you’re not going to convince somebody who’s either on the fence or leaning in the other direction, that just because the ice sheet is melting faster than expected, they should spend more money on their investment. That can’t be the reason why we convince someone … to do something different. It has to be grounded in the numbers, the value and either increased life of the asset or some other factor that convinces them from the business side.”
Burke also says that dissipating federal funding and standards for sustainability under the Trump Administration—along with decentralized sustainably efforts—are forcing national firms such as Suffolk to create a “catalog of solutions depending on geography” as well updated energy code and regulatory requirements “just to make sure we’re meeting the baseline components of what if faced by a project “going through the approvals process in any one of these given markets.”
Burke doesn’t believes owners will walk back climate and sustainability commitments “completely. For many, it’s going to continue to be business as usual.”
In a previous role as Consigli Construction director of sustainability, Burke developed its first ever carbon neutrality benchmarks and goals and achieved International Living Future Institute certification. He also played an active role on the first net-zero hotel in the U.S., Hotel Marcel in New Haven, Conn.
“That was a unique process to do a retrofit, a reposition, because it was originally an office building being transitioned into a hotel, a historic project where you could not do anything to the exterior,” he says, and it was seeking passive house and net zero certification. “With passive house, there’s a big emphasis on air sealing and air tightness, which further complicates the fact that you can’t do anything to the outside. It all has to be done from the inside.”
Burke also helped form the national Sustainable Construction Leaders network— in partnership with BuildingGreen and STO Building Group—after being part of a similar one for design leaders. The new group now consists of 60 U.S. sustainable construction professionals.
At Suffolk, he also works with climate tech companies through the firm’s start-up accelerator and the technologies group.
Burke notes his collaboration with tech innovator Sublime Systems. “It makes a cement replacement product that runs on an electrical manufacturing process, so it significantly reduces carbon emissions associated with the most carbon intensive material in concrete, which is cement, and it’s a one for one drop in replacement with cement limestone products,” he says. “It’s encouraging, as somebody who co-chairs a low-carbon concrete group in the Boston area, to see this local solution becoming available, and the amount of interest in it.”
Post a Comment
You must be logged in to post a comment.