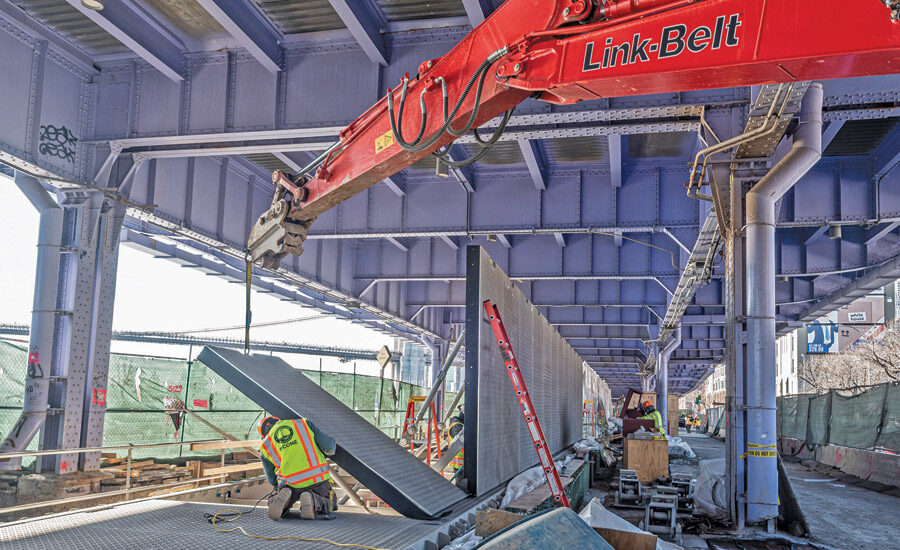
NYC’s $1.7B Investment Aims to Reduce Flood Risk
✕
Under a nondescript overpass on FDR Drive in the lower-right tip of Manhattan, a $550-million construction project is steadily advancing toward its scheduled fall 2026 completion date. Hemmed in by the parkway above and the East River at the side, it appears to be a small, almost run-of-the-mill effort, but it’s anything but.
The Brooklyn Bridge-Montgomery Street Coastal Resilience project is a key part of a multibillion-dollar program that includes elevated roadways, shoreline extensions, new green spaces, floodwalls and flood gates—all to prevent sea level rise and heavy rainfall from overwhelming and destroying critical buildings, roads and utilities in the city.
Coastal Resilience
The project, spanning 0.82 mile in Manhattan’s Two Bridges neighborhood, includes a combination of floodwalls and deployable flip-up barriers that will protect the neighborhood from storm surges and rainfall at the 100-year level in the 2050s.
It’s a vital link in the Lower Manhattan Coastal Resiliency Program that spans the borough’s lower coastline and also includes the Seaport Coastal Resilience, Battery Coastal Resilience and Battery Park City resilience projects, which will receive more than $1.7 billion in city, state and federal investments.
Together with the $1.45-billion East Side Coastal Resilience project that also is now under construction, the initiatives will protect more than three miles of East River waterfront from flooding.
“We’re not just building a flood wall. We’re creating coastal resilience,” says Greg Knabbe, project manager for John P. Picone Inc., prime contractor on the Brooklyn Bridge-Montgomery Street project.
The city’s Economic Development Corp. performed most of its design, the Dept. of Design and Construction is overseeing construction, and M&J Engineering is owner’s representative for the project. AECOM performed early modeling and other consulting services.
The Economic Development Corp. performed most of the early design because it owns most of the waterfront property where the project is located.
But because the Dept. of Design and Construction was already managing the East Side resilience project to the north, the city decided to involve the department in further project design and implementation oversight so agencies and teams “can work in tandem and be well coordinated,” says Bobby Isaac, assistant commissioner.
Flip-up gates, which are activated in extreme storms, are designed to lay flat in normal weather conditions.
Renderings courtesy of NYC DDC
Last Line of Defense
To date, Picone has installed 32 of 89 custom-designed mechanically operated gates. Most of the time they lay flat on the ground and can be walked on as part of an open public space. Under extreme weather conditions, however, the gates can flip up to provide protection against storm surge and flooding.
Gates vary in size and were designed and manufactured by Bellaire, Texas, firm FloodBreak. They seal edge-to-edge across a long alignment without any physical posts or interruptions, says Lou Waters, the firm’s president and founder.
“What this means is that each gate becomes a living member holding its own load independently while working with the gate on each side of it to provide a continuous wall up to 13 feet high across hundreds of feet of linear space—without any fixed walls or separate structural supports,” he says.
Because the gates will serve as a vital line of defense in a densely populated area, the project team requested a pilot study to verify they would work prior to awarding the contract to FloodBreak.
“Each gate becomes a living member, holding its own load … “
— Lou Waters, President & Founder, FloodBreak
In May 2022, the firm simulated various flood loading scenarios as well as debris and vehicle impacts on the gates in a testing chamber nearly 15 ft deep.
The gates performed as anticipated, and testing enabled the manufacturer to refine mount points and assembly techniques, Waters says.
Gate designers were able “to study the multiple joints and anchor points involved to further refine the design to be both robust and maintainable,” using data from the pilot test, he says.
One major challenge was the logistics of shipping gates measuring up to 13 ft tall and over 40 ft long from the Texas manufacturing location to the New York City project site. FloodBreak is currently producing gates in sections to ship them in pieces, stacked on a standard semitrailer and assembled at the jobsite. The gates, which will cover roughly 3,000 linear ft, are made up of 555 individual sections.
The flip-up gates will align with concrete wall roller gates and two swing gates along the waterfront. All will sit atop a 15-ft-deep, 3-ft-wide barrier, or sill, to prevent water intrusion under the above-ground protection.
Jet grout, in which cement is blasted into bored holes at a high speed, is being used for about 85% of the sill. But flowable fill is being used in areas where drilling holes is not feasible because of existing utilities or other materials in the soil.
With little more than 20 ft of headroom to work in, the construction team made modifications to project implementation plans.
Photo courtesy of John P. Picone Inc.
Challenges
The tiny site footprint and proximity to a busy area with many residents has required the project team to develop some work-arounds.
With limited headroom to move and bring equipment to the site—about 20 ft—as well as legacy and working underground utility infrastructure that cannot be moved, the team is using micropiles rather than normal piling to provide support for the gates and excavated areas.
Additionally, an interceptor sewer crosses under the jobsite about 40 ft down. It collects up to 40 million gallons of sewage daily from various locations in surrounding neighborhoods, so it “has to remain live at all times,” Picone’s Knabbe says.
“Digging a 40-foot by 40-foot by 40-foot excavation in the middle of a street in lower Manhattan under the FDR is difficult enough, and now you have a 12-foot to 15-foot-wide critical structure passing through the middle of the excavation. You can’t mess up that sewer,” he adds.
Normally, a bypass forced pump would be built to allow sewage to continue to divert around the excavated areas, but the hemmed-in project site lacks the room for needed equipment. Instead, the project team has developed an installation sequence that will use a gravity bypass system to divert sewage flows during construction.
With the site already being excavated, the team is also upgrading all underground facilities—which include water mains, electrical wires, gas mains and telecommunication infrastructure at the project site, according to Shahram Jaromi, senior vice president of M&J Engineering.
Isaac from the city design and construction agency says the entire team has worked seamlessly to overcome project challenges.
“Although we are tight at the waterfront, it’s a great collaboration between the three teams here and the city agencies,” he says. Participants know the limitations and “what can and cannot be done, and they are accommodating it.”
The different components of the project are designed to work together to provide a solid line of defense against flooding.
Map courtesy of NYC DDC
*Click the map for greater detail
Ready for the Next Superstorm Sandy
Agency spokesman Ian Michaels adds that the project team has worked hard to engage the community and minimize disruptions.
Local residents often ask if the project will work as the city hopes it will, he says.
With sea levels anticipated to rise by as much as 2.5 ft by 2050, and extreme events like Superstorm Sandy in 2012 expected more frequently because of the climate crisis, the project is critical, particularly in the lower-lying areas of Manhattan.
“It only has to work once,” Michaels says.
Post a Comment
You must be logged in to post a comment.