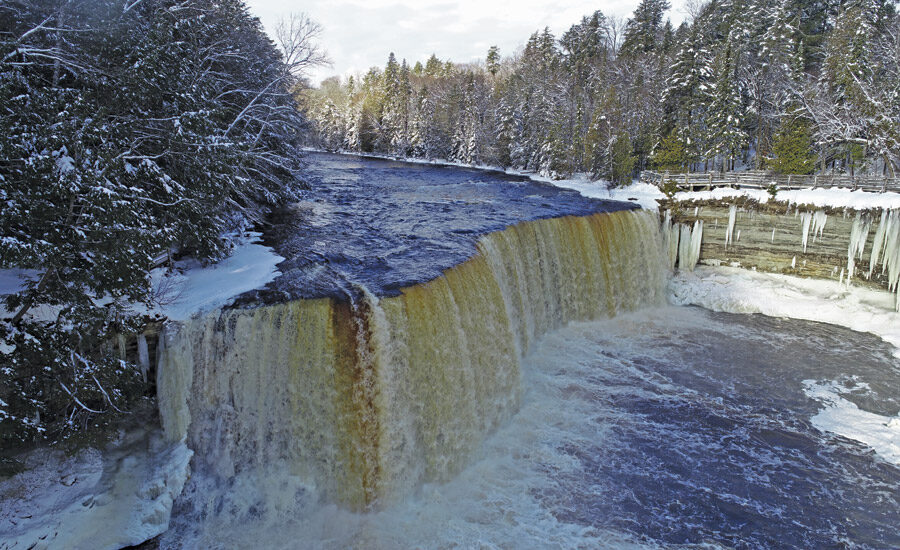
Helicopter and Hand Tools Help Expedite Park Projects
Work at Tahquamenon Falls State Park in Michigan’s Upper Peninsula are allowing universal access to a rustic island nestled in a river and to a viewing platform perched on a hill overlooking the Upper Falls—the largest waterfall in Michigan, an attraction that draws 500,000 people to the park annually.
The two projects—with some work completed and some ongoing—total only about $4 million in cost, but they were not easy to accomplish given the overriding need to protect a sensitive natural environment.
Crews couldn’t use a crane so they installed an aluminum truss bridge by helicopter over the Tahquamenon River to access the Lower Falls Island. Using only hand tools, they also removed an existing wooden staircase in order to construct a fiberglass grate boardwalk. They also are building an observation platform on a slippery, steep hillside at the edge of the Upper Falls.
The first project entailed extending a 2,000-ft-long boardwalk another 340 ft and installing a pedestrian bridge over the Tahquamenon River to connect an island in the river with the mainland.
“There was no existing bridge there previously,” says Zane Hyrkas, project manager for OHM Advisors, which designed both projects. “In order to access the island, visitors would have to row across the river.”
His firm was challenged to design a bridge that could be placed by helicopter in order to protect the area’s natural environment.
A helicopter was needed to place segments of a bridge that connects a river island with the mainland.
Photo courtesy of OHM Advisors
Meeting Boardwalk Weight Limits
Crews used the old wooden boardwalk to access the site where the new wood boardwalk and bridge were installed.
“We were limited to about 1,500 to 1,700 pounds [on the wooden boardwalk] because we didn’t know how strong the boardwalk would be,” says Steve Olsen, project manager with the contractor Olsen & Olsen Building Contractors in Manistique, Mich. “It could pretty much handle a four-wheeler with maybe a 1/2 yard of concrete. All the material had to be four-wheeled or wheel-barrowed to the location.”
To enable a compact walk-behind loader to meet the weight limit, the team removed the front bucket and front arms.
“It took six to eight guys to put it back together so we could have that machine to use on the island and for other things,” Olsen says.
Installing the new bridge required pouring two concrete pads, one on the island and one on the mainland.
To get the concrete to the island, Olsen created a cable and winch system over the river.
“I searched for a fast-speed winch, but I couldn’t find one so I actually fabricated it,” Olsen says. “I used a boat winch, and normally where you’d have put the hand crank I took that off and welded that and used that to bring the empty material container back.”
A crew prepares the concrete foundations at an observation platform that is being installed at the Upper Falls.
Photo courtesy of OHM Advisors
Bridge Installation
The project’s greatest challenge was installing the bridge, which required using a helicopter that dangled a 150-ft-long cable to carry the four, 8,000-lb segments lowered one by one into place.
“We had to get a helicopter that was big enough to pick up 8,000 pounds,” Olsen says.
The park was closed for one day so the bridge segments could be attached to the helicopter in a parking lot. Each trip was about a half-mile one way and required precise calculations that included how much fuel was needed.
“We had to get a helicopter that was big enough to pick up 8,000 pounds.”
—Steve Olsen, Project Manager, Olsen & Olsen Building Contractors
“They had to calculate just the right amount of fuel so they could bring it to the spot, give it time to set the segment and come back and land the helicopter,” Olsen says.
The crew needed to place the bridge in one day or risk paying the cost of hiring a helicopter again.
“There was only a small window of opportunity to get this thing picked up, set and assembled,” Olsen says.
It was a windy day when the bridge was placed, which turned out to be an advantage because the bridge segments were long and heavy and the downward pressure of the rotor wash, which pulls air from above and pushes it downward to create lift, helped nudge the load downward.
“The wind was actually a blessing because it gave them better lift,” says Kevin Dennis, park manager.
wind had died down by the time the last segment was placed, which turned the experience into a nail biter for the ground crew waiting to bolt it in place.
“[The pilot] was trying to pull up the helicopter, but he couldn’t because the wind from the helicopter pushed the bridge piece so much that he couldn’t lift it,” Olsen says. “He had to go back and add 100 feet of cable so he had greater distance between the bridge and the helicopter. When he did that, he was able to set the last section.”
Olsen calls that moment “nerve-racking because if we couldn’t set that last section I would have had to search for a larger helicopter. They do make bigger helicopters, but it would have cost significantly more.”
Olsen had one crew hooking up the bridge sections to the helicopter and another on the river attaching the sections.
“We had to bolt everything tight because if the bridge had even a little bit of a gap we wouldn’t have been able to set that last section,” he says.
Olsen says it’s the only time his company has used a helicopter in a project, and he’s not sure he wants to do it again.
“We [usually] set things with cranes, and with cranes you can slowly set it down like a quarter inch at a time. You can really manipulate it,” he says. “But here, the pilot was battling winds and battling lifts. So it had to be kind of fast process.”
Before the bridge was installed, visitors had to row a boat from the mainland to the island.
Photo courtesy of OHM Advisors
Upper Falls
Just as with the bridge and boardwalk project on the Lower Falls, another project being built on the Upper Falls requires the use of hand tools—the replacement of a 94-step stairway that descended the hill in nearly a straight line. In its place, a fiberglass grate ADA-friendly boardwalk will zigzag in an expansive pattern down the hill to where an observation platform will be replaced overlooking the falls. The boardwalk will have five switchbacks with landings and benches.
“Sometimes you sit down and you rest and reflect and you’re surrounded by nature and you just take it all in.”
—Alex Kish, Project Manager, ASI Environmental
The project is challenging, says Alex Kish, project manager for Ludington, Mich.-based ASI Environmental, because “there’s no flat place to gain footing. And there’s not a way to get machinery in so a lot of the work is being done by hand and, in some of these spots, you’re working in 10 inches of muck. The ground is trying to pull your boots off as you step.”
“It’s a very steep and dynamic hillside and has pockets of wetlands,” agrees Hyrkas. “And by dynamic, I mean that the material on the hillside slowly creeps from the top to the bottom—as gravity would.”
The construction team is installing 425 footings for the ramp, all 18 to 24 in. in diameter. To cope with the dynamic hillside, the crew is using two foundation types: Sonotubes, which are cylindrical-shaped tubes used for forming concrete columns, and helical piers, which are being installed on the upper third of the boardwalk.
“The concrete foundations are anchored directly to the bedrock in order to resist the downward movement of material,” Hyrkas says.
Work continued through the winter on the project, which started in October and is slated to be done by the end of July.
By using a ground-thawing device featuring a circulating hose with antifreeze running through it and covering it with thermal blankets, the team kept the ground warm enough in the footings and foundation holes for the concrete to cure during the winter months.
The team removed the previous observation deck but kept the existing stairway that was built in the 1970s in place to maintain access to the area. The new observation deck will have an 11-ft to 12-ft-long cantilever supported by steel beams.
The cantilever is needed, Hyrkas says, because the waterfall causes the sandstone bedrock over which it flows to erode. He says it has eroded 13 ft from the hillside since 1974.
Crews install a helical pile for a new ramp that will lead to an observation platform overlooking the Upper Falls.
Photo courtesy of ASI Environmental
“The new platform is designed with a cantilevered steel beam superstructure so that when erosion occurs, and the cliff erodes back and gets close to undermining the foundation, they’ll be able to pull the viewing platform back and set it on new foundations. They can move it backward as they need to,” Hyrkas says.
Dennis says the project is further complicated because “their work zone is only as wide as the footprint of the boardwalk.
“If we just let them work willy-nilly, we might have a beautiful boardwalk, but, at the end, the hillside would have all kinds of problems with erosion.”
While Kish says the project has been brutal, it has also been beautiful. “It’s taken a lot of grit—that’s what has gotten us through—some very hardy crews and tough guys sticking at it day after day,” he says.
It helps when “sometimes you sit down and rest and reflect and you’re surrounded by nature and you just take it all in,” he adds.
Post a Comment
You must be logged in to post a comment.