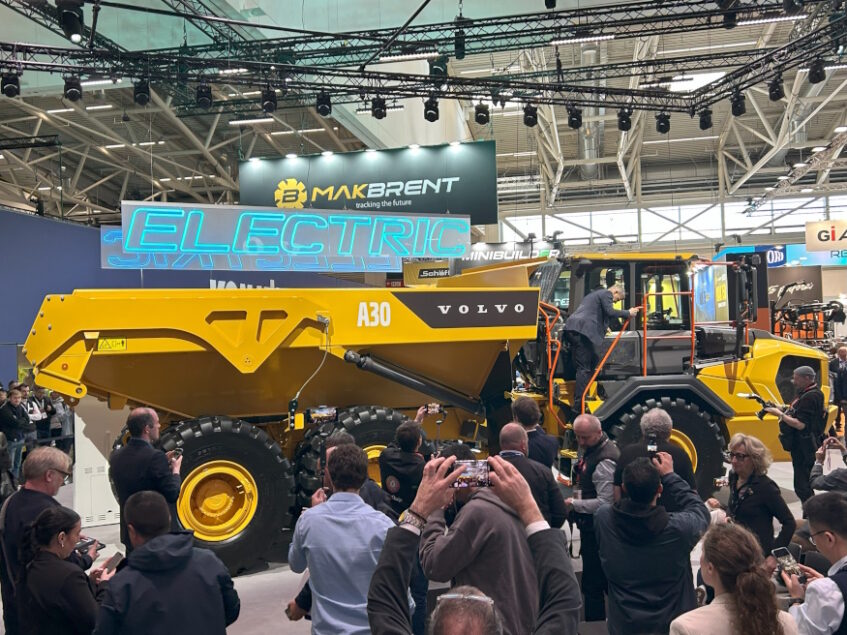
Volvo, Case Press Forward on Fully Electric Equipment at Bauma 2025
Volvo Construction Equipment unveiled its first all-electric articulated dump trucks, electrified versions of its A30 and A40 trucks,
at the Bauma equipment exhibition in Munich, Germany, April 8.
Case Construction Equipment and electrification supplier Moog also unveiled new electric equipment news at the conference.
The A30 Electric articulated haul truck was revealed at Volvo’s April 8 press conference, the world’s first serial-produced, battery-powered electric haul truck of its size. It will be available along with a larger A40 electric haul truck for customers in some European markets in 2026. The A30 is sized for construction, mining and quarrying customers and Volvo CE CEO Melker Jernberg said that after Volvo CE introduced an electric version of its EC350 excavator in 2019 and an electric EC230 excavator in 2020, Volvo was ready to tackle the largest consumers of carbon-heavy diesel fuel on construction sites, the trucks whose beds those excavators fill. Volvo CE is targeting 35% fully electric sales by 2030 and hopes to achieve net-zero greenhouse gas emissions across its entire value chain by 2040, goals that Jerberg admitted the market is moving too slowly on for the manufacturer to achieve them.
“The transformation is underway, unfortunately, slower than expected, slower than needed, slower than than wanted,” he said. “We have decided that we need to continue now to lead the way when it comes to sustainable solutions for transport, for construction, for infrastructure. To make that happen, we need different technology solutions.”
Jernberg and other Volvo execs said the company will invest heavily in hydrogen fuel cell technology and even in cleaner internal combustion engines that customers are not ready to move on from as well as continuing its all electric equipment investments. He said the internal combustion engine will continue to play an extremely big role in the construction industry, and Volvo will continue to invest in it.
“Battery electric will be the main path for Volvo trucks to reach the net zero,” he said. “The Volvo Group was very early out with electric. We started with buses. Now we have a full range of electrical trucks available for all customers around the world and a full lineup of electric construction machines.”
The company said Volvo’s electric highway trucks have driven 99.4 million miles worldwide to date. The A30 unveiled at Bauma has five lithium-ion batteries encased in its front cab compartments chargeable by onsite generators or storage units. Volvo said the A30 can run for four to five hours on one charge doing most construction tasks but they conceded runtime may drop on heavy construction tasks such as moving loads of rock at high rates of speed on road building projects. Less demanding tasks like going downhill, ones that allow Volvo’s energy-saver technology to take over, could see one charge last as long as seven hours, they said. Volvo CE’s lithium-ion batteries can be charged from 20% to 80% in about an hour, Jernberg said. Operators can check charging status, machine hours and energy consumption using Volvo CE’s My Equipment app on site or remotely.
The company estimates carbon-dioxide reductions of 84% for the electric A30 and 90% for the A40 for the two large trucks’ lifespans after they are released in 2026 compared to their diesel versions.
Case Brings in ZQuip
Case Construction also focused much of its Bauma energy on its range of electric equipment. The company introduced the CX210ZQ, a full-size electric excavator developed with Moog battery electric technology, including a modular ZQuip battery system that enables rapid battery swaps with lithium-ion battery packs that can be slapped into slots on the back fo the excavator.
Case’s CX210ZQ excavator is powered by swappable ZQuip battery packs.
Photo by Jeff Yoders/ENR
“Innovation is our foundation,” said Fabrizio Cepollina, Case CE vice president for EMEA region and global alliances. “It’s ingrained in our DNA. Since 1842, innovation has been our driving force, ensuring our continued vitality. For Case, innovation means delivering practical, impactful solutions, products and services, that directly enhance our customers’ businesses.”
The partnership with Moog on its ZQuip aftermarket battery system extends beyond just the CX210ZQ as Moog is providing electric actuators and other systems to achieve full electric operation of Case’s machines. Moog has a similar partnership with Bobcat. It’s partnerships with OEMs also involve machine guidance and automation beyond basic electrification.
ZQuipped for Construction
At its own booth, Moog showed off its new generation of fully electric equipment including the Bobcat and Case machines and even a Volvo loader converted with TerraTech sensor and energy load management technology. Moog’s previous generation of full conversions to electric were achieved through replacing engines with battery packs in the engine compartment of a loader, excavator or skid steer, with a series of large wire connections and glycol hoses for coolant connected the battery packs to actuators, cab controls and coolant reserves.
Moog’s new electric cabinet, the adaptive electrification management system, has seven swappable batteries that connect DC power to all functions of the machine with a universal base plug in at the back of each battery pack.
Photo by Jeff Yoders/ENR
Moog’s new generation of battery packs known as the adaptive electrification management system, unveiled at Bauma, are connected in a simple cabinet to distribute electricity and coolant. The batteries come in individual packs and can be swapped in or out of the cabinet the same manner that toner cartridges in a printer. One connection in the back distributes DC power to the machine. The cabinets house at least five of the individual battery packs and can power a loader, small excavator or skid steer for up to eight hours depending on how many batteries are used and the size of the individual machine’s engine compartment.
The Volvo TerraTech loader Moog demonstrated integrated sensors for recording everything from energy consumed to rock moved.
Moog’s TerraTech loader takes electric technology beyond powering the hydraulics and motors to using sensors to measure load weight.
Photo by Jeff Yoders/ENR
“Because all of these electric motors and cylinders and actuators have sensors in them, you can tell at any point in space where that bucket is,” explained Bill Perry, Moog spokesman. “You can also use the auto load feature to know how many lbs or kilograms of stone you have in the bucket and it will shake it and weigh it until it gets to the proper weight.”
Post a Comment
You must be logged in to post a comment.