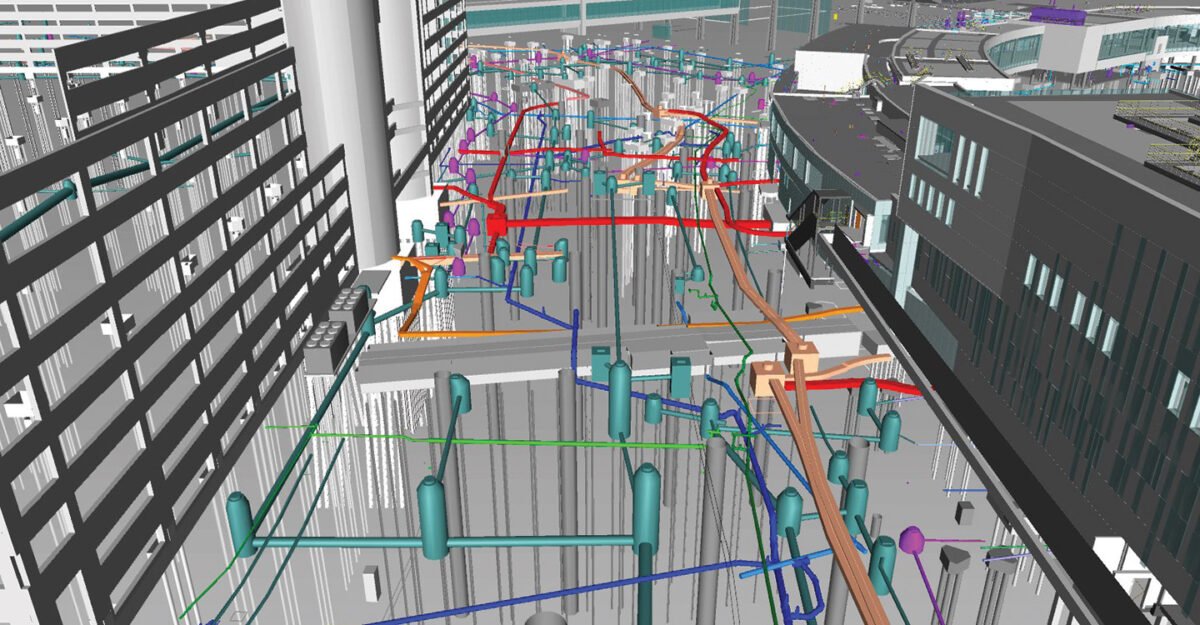
Tech tools Enhance Asset Management
✕
Shortly after she took the reins at the Massachusetts Port Authority for capital programs and environmental affairs, Luciana Burdi asked her team to envision how technology could be leveraged to easily access information about the agency’s infrastructure assets—more than 200 buildings and utilities across three airports and multiple marine facilities.
“I have been in the industry for 25-plus years, and have noticed that in any large organization, there are always challenges in compiling information,” says Burdi. “It’s not missing—it’s just not easy to access. The technology is there, and I’m always trying to leverage it to solve real problems. Once we have this information, how do we start visualizing it in a way anyone could use?”
In 2021, Massport launched MICA (Massport Infrastructure Condition Assessment), forming a 9-person advisory panel representing key Massport departments and a core team of project and facility managers and subject matter experts (SMEs). One key goal was to better understand building conditions in order to achieve the agency’s mission of reaching net zero by 2031. “Originally, the idea was just to get a dashboard of these details,” says Burdi. “Then we realized that utility infrastructure is another big can of worms to open.” For example, if there was a water main break, the team would check available data on that pipe and “once we dig further, we might see that the line is 30 years old. How many other lines do we have that are that old? When do we start looking at replacing them?”
Zachry is utilizing AI-driven ALICE Core technology to create visual representations of construction schedules and modify accordingly, as on the State Highway 114/121 corridor near DFW airport.
Photo courtesy of Zachry
The agency brought on the data and digital solutions consultant Keyrus, says Mark Ricketson, Massport program manager for design and technology integration. “A holistic view of all the conditions and utilities had never really been done. We were reactionary—if a utility breaks, we fix it. In this case, we’re being more proactive.”
HNTB led the buildings assessment process, using the project management framework Scrum to make it as agile and streamlined as possible, says Aaron Ford, HNTB’s IT section manager for program delivery. That was key for gathering data about facilities located in secure areas at the airports. “We needed to maximize the time” allowed for being in those secure areas, he notes.
Instead of using the linear, sequential, “waterfall” approach, the team utilized Scrum and the lean construction approach to continuously optimize the process by delivering “sprint” updates every two weeks, adds Kathryn Garrett, HNTB project manager. “It was an idealistic—and moving—target to assess 171 buildings in two years. Scrum allowed us to manage expectations.”
The team broke down building data into 15 disciplines and documented and rated conditions of individual assets such as pipes, doors and windows. Just the physical work of collecting data was challenging, says Garrett. “Sometimes the as-builts were on a project manager’s desk; just identifying the right person to ask could be a challenge.”
Nancy LaFarge, HNTB technology section manager, facilitated coordination between inspectors and SMEs, and refined the 15 survey types—architectural, structural, systems, codes, sustainability, etc.—accordingly. “Once SMEs and field inspectors were on the same page about what data was needed, the surveys evolved,” she says.
Stantec came on board to assess 41 utility systems. “We started with a robust series of interviews,” says Jennifer Ducey, Stantec vice president for transportation. The team interviewed personnel from managers to people out in the field. “We tried to understand ‘what information do you use, need and want,’” she says. After gathering as much data from reports and plans as possible, the team created a lifecycle asset management curve “where we assigned a base condition rating to as many assets as we could,” she says. “If we knew the installation date and material, we applied an expected lifespan of that utility.”
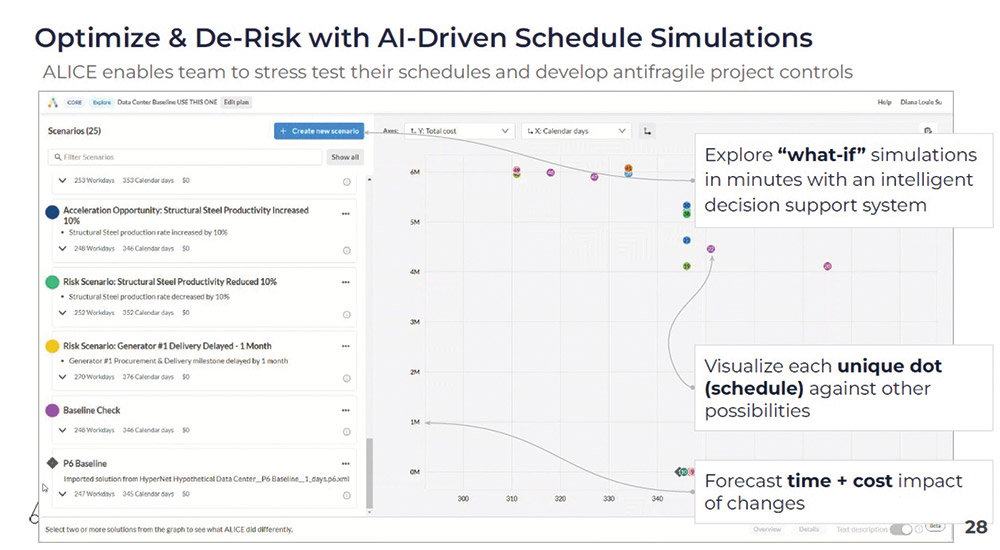

ALICE technology offers contractors a clear view of construction scheduling and insights into what needs to be adjusted according to labor, materials and other factors.
Graphic courtesy of Alice Technologies
Keyrus had to take all the data from various sources and move them into a central depository, notes Arsalan Malik, Keyrus technical project manager. “The goal was to move data from ArcGIS [software that uses geographic information to create maps] into a central repository, then create a dashboard to visualize the data.” The team used the cloud platform SnapLogic to integrate the data, Snowflake to store, process and analyze it, and Tableau for data visualization and “a dashboard solution where users go for day-to-day work tasks,” he adds. “SnapLogic and Tableau were already used at Massport; we worked with them to utilize the best of those,” he says.
In its first two-year phase, MICA has generated almost 3,000 recommendations for improving infrastructure and energy efficiency, and “fourteen projects that we had no idea we needed,” says Burdi.
In Phase 2, rolling out this year, Massport and its consultant teams will focus on scaling MICA up for more business use cases and types of assets, with the ultimate goal of creating a digital campus. “We define a digital twin as a smart building system,” says Ricketson, envisioning a time when “an asset will tell us, ‘you need to check me out’ or ‘there are too many people in the room, so turn down the heat.’” MICA may eventually allow staff to quickly find the overall condition of a facility, then drill down to its individual assets.
Keyrus has worked with other transportation agencies on similar efforts, says Stephanie Abshire, its U.S. managing consultant. All have “the business challenge of how much data exists within the organization, how many different data sources there are, how to take all of that and make it mean something, and solve problems,” she adds.
CCTA is working with Davteq to not only get real-time information on roadway conditions and situations, but also to leverage data to identify solutions for those situations.
Graphic courtesy of Davteq
Augmenting Decisions and Road Safety With AI
Similar to Massport, the Contra Costa Transportation Authority is taking a phased, deliberate approach to using technology to inform its planning decisions. A partnership with Davteq, a firm offering data- and AI-driven solutions, began with Timothy Haile, CCTA executive director, needing to answer board members when they would ask, “Hey Tim, what’s happening on State Route 4 today?” he recalls. “In the past, we didn’t have that real-time info.”
Although CCTA already utilized technologies such as Streetlight Data, “we wanted to do a better job rather than going to five or six places for information,” he says. “Then it led to bigger conversations: Let’s build a repository and that can become a digital twin. We want to be a more performance-based planning organization.”
When faced with traffic congestion, an engineer would typically come up with a solution, then CCTA would evaluate whether it fixed the problem. Instead, Haile asks: “How can we use the data to tell us where the problems are and apply cost-effective solutions? As we build AI into it, we can start asking questions to the database and be able to get answers.”
CCTA is also looking to leverage AI to quickly identify projects, such as intersection and road improvements, that can fulfill its Vision Zero goals to eliminate traffic fatalities and prioritize grant applications. Moreover, it wants to create a countywide evacuation plan for high-risk areas where smart traffic and transit signals can be optimized and connected to city and emergency systems, adds John Hoang, CCTA planning director. As for capital planning, “We go out and plan and build, but we never go back and make sure the project did what we said it would do,” Haile adds.
Davteq takes data from sources such as Streetlight Data, state traffic detectors and 501.org to create insights and dashboards for CCTA. Those traffic stats—along with graphs and maps, planning documents, reports, traffic and incident data and project data—create a knowledge base that, when enhanced by AI, can identify what road sections are most incident-prone and what trends occur before and after projects, notes Ali Mortazavi, Davteq founder and CEO.
Contractors working on large, heavy civil projects are also turning to AI to better plan everything from scheduling to procurement. Zachry is using ALICE Core, an AI-powered scheduling tool that allows users to pull in data from Oracle’s Primavera P6 scheduling software on several projects, including the $149-million Interstate 10 Graytown to Bexar County Line project for the Texas Dept. of Transportation and the $1.44-billion DFW Connector. ALICE Core has two steps: the first is an assessment phase where the system digests an XCR file from P6 and presents it in a sequence with variables labeled and linked. Labor, materials and other factors are extrapolated and presented in a visual representation of a construction schedule.
“What we’re building is a hybrid,” says René Morkos, founder of ALICE Technologies. “You can schedule in 2D. You can visualize in a work breakdown schedule and 2D. You can zoom in and zoom out of the work breakdown structure. You can draw arrows between the levels of the WBS rapidly, instead of having a sort through 6,000 tabs.”
HNTB and Stantec teams gathered as much data as possible from an array of disparate sources, including on-site investigations of buildings and utilities for Massport’s MICA program.
Photo courtesy of Massport
Work can be rescheduled and crews can be added, subtracted or even resequenced depending on potential issues ALICE Core’s AI sees with a project’s schedule.
“We’ve just started using this, and we’re already seeing much of value in the way we bid projects and the way we control projects that are live,” says Ranjeet Gadhoke, vice president of project controls at Zachry. “We’re managing resource gaps. ALICE will help us fill those gaps right and optimize our schedule.”
As part of Zachry’s digital transformation in 2013, the scheduling function was separated from projects to be more of a regionalized function of planning. “We have professional schedulers building the schedule, and I know how many gaps we still have and what it takes to overcome those inefficiencies” Gadhoke says.
ALICE Core allows Zachry’s schedulers to run multiple iterations to present multiple options to the operations team. “We’ll be sitting with the superintendent and say ‘you know what? It’s okay to delay this operation, but if you delay it by one month, you’ll get continuous work without having inefficiencies in labor. That’s powerful,” Gadhoke says.
The Michigan Dept. of Transportation, which has the advantage of close contact with domestic automakers and technology vendors, has four AI pilot projects involving road safety in the works. One uses AI for several different safety measures as well as cameras and other technology to warn bus drivers and other equipped vehicles of potential hazards, such as pedestrians and cyclists. Another system uses flashing road signs to alert wrong-way drivers on ramps to I-75, I-375, and I-696.
“Once they go past that [system] we activate some signs and lights so a driver would know what’s going on,” says Michele Mueller, manager connected and automated vehicles and electrification at MDOT. “When they cross a second threshold is when we actually put alerts out to the state police and our operations center to take action.”
Mueller notes that use of such safety AI systems has become commonplace for state DOTs. When workers are present, motorists will receive notifications to reduce their speed for safety purposes. She adds that most of the AI systems MDOT uses for safety are related technologies that can perform several safety verification tasks, and MDOT has an open dialogue with automakers and technology vendors about what works and what doesn’t.
Many of the notifications work with the technology built into the automobiles’ CPUs, and some go directly to apps that drivers can legally use in hands-free mode with a mounted cell phone. Other notifications are programmed into their existing network of interactive signs. All driver and DOT data that the system gathers or uses is anonymized and not available outside of the internal database.
MDOT is partnering with Cavnue on a 3-mile pilot on a stretch of Interstate 94 near Ann Arbor. The goal is to create a technology-enabled road that communicates directly with autonomous and regular vehicles and driving apps. The project is designed to improve safety on the corridor, reduce congestion, improve mobility and make better decisions about different types of traffic. Testing is done in the left lanes in off-peak hours using poles outfitted with radar, sensors and wireless radio equipment.
The goal is to gather information and deliver it to drivers faster, Mueller says, and “to make our response faster as well—whether it’s to an incident, debris or any of the things you might run into on the road.”
Post a Comment
You must be logged in to post a comment.