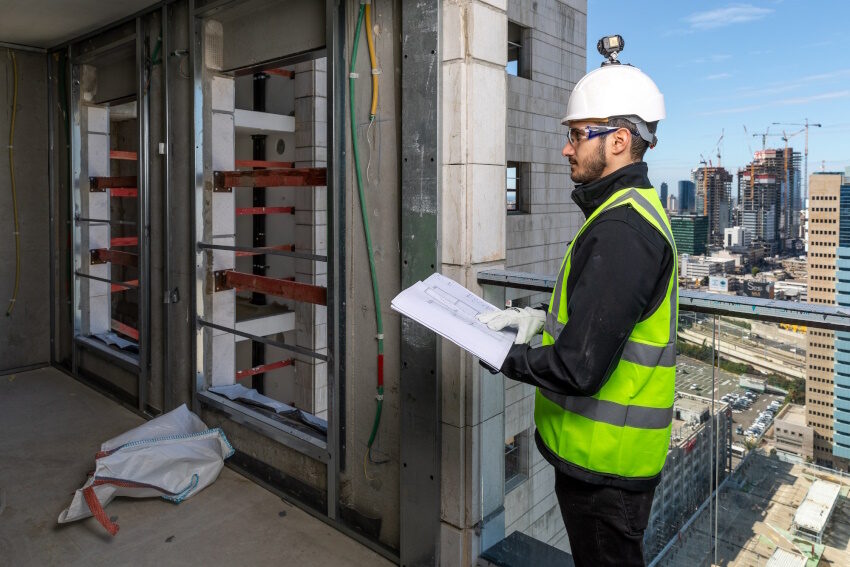
Predictive Analytics Promise the End of ‘Gut Feelings’ in Construction
The construction industry stands at a crossroads. With skilled labor shortages, rising costs, and increasing project complexity, traditional approaches to project management are showing their limitations. Predictive analytics offer a path forward — not by replacing human expertise but by augmenting it with objective data and early warning capabilities.
Replace Subjective Reporting with Data-Driven Progress Tracking
The evolution toward predictive analytics represents a fundamental shift in construction process management. Rather than simply documenting what has already occurred, predictive analytic systems analyze trends and identify potential issues before they become critical problems.
Nonetheless, building trust in artificial intelligence-driven data remains a crucial hurdle, with project teams skeptical about how it could be possible for AI to track all of the complexities, and how accurate the data actually is. One planner’s skepticism even led him to conduct his own cross-check, manually measuring rough-in drywall installations against what his newly-acquired AI progress tracking system had reported. After two hours of calculations using scale rules and measuring plan quantities, he found a difference of just 2% in reported progress.
Most project managers would probably not go to those lengths, but for this man, manually discovering that level of accuracy helped establish confidence in the system’s capabilities.
We at Builbots are seeing that many professionals are finding that their relationship with technology works best when they remain actively involved in the data collection process. By conducting walks of the site while collecting data, planners maintain their connection to the physical space while benefiting from the analytical capabilities of AI systems.
After these types of walks, “you’re kind of more connected to it and you’ve got more reason to accept it or challenge it,” according to Lee Howlett, a professional with 20 years of industry experience who’s currently a planner at top UK-based construction company Sir Robert McAlpine.
Transform Supply Chain Relationships
Data-driven project management also reshapes relationships with subcontractors and supply chain partners. When everyone has access to the same objective data, conversations shift from opinions and finger-pointing to collaborative problem solving.
“If you’ve got an objective data set that’s transparent, the supply chains see it, hopefully the customers see it… you’ve just got the truth and everybody sees exactly the same data,” Andy Pritchard, head of technical at Willmott Dixon Interiors noted. “That transparency is the key. Everyone’s looking at the same problem.”
This shared reality creates a foundation for more productive discussions about performance and resource allocation. Rather than relying on subjective evaluations that can vary significantly depending on who’s doing the reporting, teams can have fact-based conversations about outputs and timelines.
Support, Not Replace, Human Judgement
Some construction professionals have concerns over how technology — particularly AI — will impact their roles and teams, particularly when it comes to skill erosion. But in successful predictive analytics implementations, technology enhances human capabilities rather than replaces them.
“What we’re really worried about is: what effect will it have on our short-term planning, on our conversations and on our project managers really owning that program?” Pritchard acknowledged. “At the end of the day, we’re just trying to manage humans. We’ve got 1,000 builders on site, 100 people in the site team, whatever it is on that job. It’s all about communication between them and if we just rely on the system and the data we start losing that ability to communicate a bit.”
Technology must be viewed as a partner that handles data processing while leaving decision-making and relationship management to humans. Predictive analytics can identify potential problems and suggest solutions, but it takes experienced professionals to determine the best course of action and coordinate the resources needed to implement solutions.
This can be especially impactful during the earlier stages of a project, in terms of improving timelines and efficiency, as well as critical inter-stakeholder relationships. “In construction, we often find ourselves in very stressful situations,” according to Jeremy Cortesio, project executive at Skanska. “As a management team, we can help people avoid this by incentivizing them to plan and track things in a way that focuses on the front end of projects.”
Predictive Tendering
With the human touch, benefits of predictive analytics can also extend beyond current project performance. The data collected creates a valuable repository of information about actual construction outputs. This information can inform pre-construction planning and tendering for future projects, as well.
Planners can use data to support pre-construction teams during the tender process, by doing things like checking program integrity against outputs and identifying potential risks of delivery prior to signing into contracts.
This is significant for an industry that has traditionally struggled to systematically implement lessons learned from past projects. Instead of relying on general industry output books that often differ from one another, teams can now base future planning on verified, project-specific performance data based on projects they themselves have actually worked on.
Moving From Reactive to Proactive Construction Management
The future of construction management lies not in reactive firefighting but in proactive, data-driven decision-making that allows teams to address problems before they become crises.
Many in the industry understand this and have shown it by adopting data-based technologies en-masse, and yet it is critical that people understand that as revolutionary as some new construction technologies may be, they —in and of themselves — will not fully solve all construction delays and issues.
True change and improvement must come through proper, effective and sometimes creative usage of technology by the people who are ultimately responsible for ensuring the success of their projects.
Amir Berman is vice president of Industry transformation at Buildots.
Post a Comment
You must be logged in to post a comment.