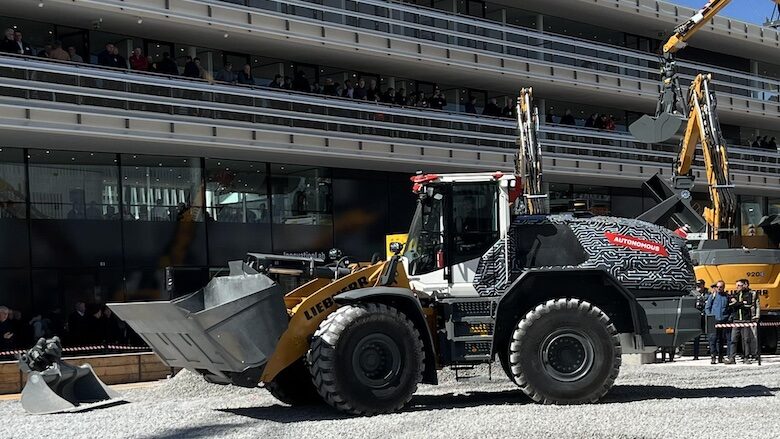
Liebherr, Volvo CE See Bright Future for Autonomous, Electric Equipment
Swiss-German equipment giant Liebherr chose the Bauma trade show in Munich, Germany, to show the current state of its years-long drive to develop autonomous construction and mining machines, showing off a wired-up generation 6 L 550 XPower 20-ton, 220-hp wheel loader.
The driverless wheel loader roared to life in the demo gravel pit outside Liebherr’s booth at the triennial trade show, executing three-point turns and depositing gravel from a pile to a loader in a clatter of rocks and dust.
There was a good deal of human input given the crowded expo space—a Liebherr official was scoping the route on a laptop in the cab before the loader went driverless, and another trailed the machine with a small black and orange control box in hand. At some point the loader made an emergency stop (because of all the mobile phone traffic in the surrounding crowd, event emcee Alexander Katrycz said) and a Liebherr employee got in the cab for the rest, though holding up his hands to show he wasn’t driving.
The nerves of the wheel loader are under control of the Liebherr Autonomous Operations system, developed in house. It runs via onboard 3D environmental sensors and, the company says, is free from the need for support from drones, separate surveying technologies or GPS. A 360° laser scanner setup is rigged around the roof of the loader cab.
The system displayed by the loader is still in field testing, spokesman Simon Truempler says, but by June or July this year the firm plans to intensify test deployments with selected customers and look for the right time for a broader market launch.
Liebherr has invested heavily in semi-autonomous and fully-autonomous machinery in recent decades as the industry as a whole pursues its dreams of always-on production that never sleeps, complains, gets hurt or wants to take vacation.
Liebherr has been working with Australian iron ore miner Fortescue, which already fields autonomous trucks in its mining fleet, to develop a scalable autonomous haulage solution to run on jointly developed all-electric mining haulers on a very large scale: with the 240-tonne T 264, with Fortescue designing the batteries and drive trains and Liebherr providing the truck body.
Tests and development on those systems are continuing at Fortescue’s Christmas Creek mine site proving grounds in western Australia. The two companies inked a $2.8-billion deal last year to field 360 autonomous battery-electric trucks, 55 electric excavators and 60 battery-powered dozers.
More broadly, there are some 2000-plus autonomous haul trucks of varying stripes deployed at surface mines worldwide, according to Engineering and Mining Journal, citing GlobalData’s Mining Intelligence Center, with the bulk of these are produced by Komatsu and Caterpillar. Material giant Heidelberg signed a deal with Pronto in February to deploy 100 autonomous haulers globally. Suncor Mine has been running Komatsu autonomous hauling trucks at oil sand sites north of Fort McMurray in Canada for nearly a decade.
But actually producing and deploying smaller vehicles and running multiple kinds of truly autonomous, driverless machines across a complicated workspace in constant motion? Those efforts are still in early days, even if the concepts are in advanced development.
Volvo’s Autonomous Electric Mining Machines Still a Work in Progress
Electrifying and running autonomous traffic in smaller-scale mining scenes like quarries and sandpits—these being more common than the ones found in the wide-open flats of western Australia and northern Canada—could be trickier.
Volvo Construction Equipment produced a self-learning battery-electric wheel-loader concept—the LX03—at the end of 2021, with the design actually developing from an initial collaboration with LEGO. It is still a work in progress.
Physicist and simulation expert Martin Servin at Algoryx and Umeå University expects the variety of soil types found in the world to continue to present challenges to autonomous hauling, mining and construction machinery. Servin and his colleagues produce physics-informed world models; he joined a small team of computer science and physicists in producing World Modeling for Autonomous Wheel Loaders, part of a Komatsu-supported doctoral program for the researcher Koji Aoshima.
“The capability to handle more complex material than uniform gravel—and to adapt to pile shape—has been an obstacle,” Servin says. The growing ability of deep learning systems to react to multimodal sensor data and simulation means they can now handle more complex material, such as fragmented rocks. “Strongly cohesive or heterogenous soil is still a challenge. So are boulders.”
In mining operations, the autonomous workspace faces further practical hurdles, says Moritz Ziegler, a senior engineer and group lead at Aachen’s Institute for Advanced Mining Technologies. “For decades, the paradigm has always been to just scale up your mining truck: to get bigger trucks, bigger payload, fewer trucks and more material transportation,” he says. “But this approach is not feasible for electrification, in our opinion, because of the payload ratio with the battery and a few other factors. You very soon run into technical limitations there.”
Ziegler was at Bauma 2025 describing some of the case studies and experiments his institution has been pursuing with partners including Volvo Group and Mineral Baustoff at brownfield sites Eigenrieden and Nivelstein in Germany. The experiments are making use of the TARA system developed by Volvo Autonomous Solutions. What’s unique here is combining electrified transport with autonomy.
He sees the potential for applications, but applying them to individual smaller-scale mining sites—each one unique—poses persistent obstacles. “If you use a high number of vehicles it can quickly get out of synch,” he says. “It’s more difficult than we thought before. You basically have to lock up the whole of the mine site where the vehicles are operating for safety reasons. It is a real complex process.”
While ramping up large-scale deployment of a wide variety of driverless machines may come in fits and starts, though, the tech is arriving. “Autonomous transport is definitely possible,” Ziegler says. “And it has arrived at the market.”
Post a Comment
You must be logged in to post a comment.