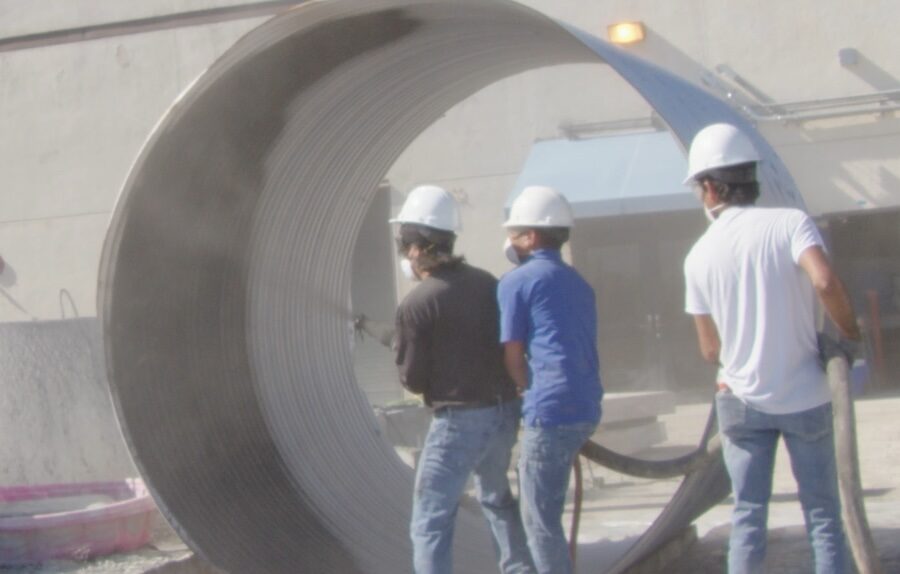
Florida Researchers Advancing Potential of Sprayable Ultra-High Performance Concrete in the U.S.
Researchers at Florida International University (FIU) in Miami are advancing a new approach to sprayable ultra-high performance concrete (UHPC), building on a successful field test to illustrate how the durable, high-strength material could offer a more practical and cost-effective alternative for structural repairs. Over the next year, the FIU team plans to build a mobile unit that houses all the equipment needed to carry out concrete repairs, from preparation to clean-up.
Already utilized in Europe, sprayable UHPC has long been touted as a faster, more efficient means to repair corroded bridge walls, columns and girder ends without the need for formwork or other elements of cast-in-place application. Though the concept is similar to the application of shotcrete, a key obstacle to wider use has been the high cost of commercial, proprietary UHPC—as much as 20 times more expensive than conventional concrete mixes, according to recent studies.
FIU, the University of Michigan, the University of Minnesota and Iowa State University all have programs that have focused on developing open-source, non-proprietary cast-in-place mixes that provide the same performance at less cost than their commercial counterparts. Professor Atorod Azizinamini, FIU’s director of infrastructure research and innovation, explains that while the mix modified for spray applications costs approximately $700-800 per cubic yard, “it’s still cost-effective because the amount you’re using is very small. Yet it provides the same performance with respect to mechanical properties and durability.”
Azizinamini estimates a sprayed UHPC coating of one inch or less may be sufficient for many routine spalling and corrosion repairs, while more deteriorated elements would require thicker coatings along with additional reinforcement.
Transforming laboratory performance into a viable spray application system for field applications has proven as challenging as fine-tuning the mix itself.
“On the surface, it seems easy,” Azizinamini says. “But when you get in the field, you’re doing large batches with varying location-specific material considerations, as well as different equipment involved in all stages of the process.”
Time is also a factor. As the mix starts to set after 30 to 40 minutes, users need to balance batch size and composition with the time available to spray.
“If you’re not careful, you risk ruining all the equipment,” Azizinamini says.
A milestone in FIU’s effort to refine its system for sprayable UPHC came last year through a collaboration with the Virgina Department of Transportation, marking the first time the process has been utilized for a concrete repair project.
VDOT district bridge engineer Sam Fallah explains that as with other agencies, structural concrete deterioration resulting from the use of highway de-icing salts is a longstanding maintenance issue.
“Repairing vertical surfaces with conventional cast-in-place concrete requires no less than 4 to 6 inches, which adds weight to the foundation,” Fallah says. Along with being a more efficient application process, he adds, sprayable UHPC can armor structure to protect further intrusion.
VDOT chose to test FIU’s sprayable UHPC system on an exit ramp bridge within the Capital Beltway/U.S. Route 50 interchange in Fairfax. Built in 1985, the structure’s abutments evidenced spalled concrete and exposed, corroded rebar resulting from joint leakage.
Photo courtesy of FIU
Conducted last August, the test team prepared an approximately 20×8-ft area by removing delaminated and unsound concrete through sand- and waterblasting. FIU’s team then sprayed four layers of UHPC to build an average thickness of one inch. Each layer required approximately three minutes to apply.
Although plans to repeat the test on the opposite abutment were curtailed by mixer size limitations, Azizinamini was pleased with the results, noting that a follow-up visit to the site earlier this year revealed no further deterioration, though VDOT had subsequently applied a coating to the area for aesthetic purposes.
“Where aesthetics are not an issue, the resulting rough surface is fine as is,” Fallah says. “Any coating or smoothing can be done at the same time as the application.”
Though impressed with the system overall, Fallah says the process needs to be standardized. “The typical highway worker needs to be able to gain the skill to apply it correctly,” he says.
Azizinamini agrees, noting that while UHPC is a cementitious material, the spray process needs to be approached as a system that requires a well-trained team to execute properly.
“Even a small deviation from the required steps will cause the whole process to collapse,” he says. “It’s not something you can learn by reading a manual or watching a presentation; it requires hands-on experience.”
Developing that expertise using the planned mobile unit will be the next step of FIU’s research effort, thanks to a federal grant awarded through the South Florida Risk + Resilience Tech Hub to commercialize the sprayable UHPC system.
“We’ll use the mobile unit to conduct workshops across the country for contractor training,” Azizinamini says, adding that the sprayable UHPC system should be feasible for any type of constructed facility—bridges as well as buildings.
“In all our experiments, we’ve yet to see a failure at the bond,” Azizinamini says. “It’s allowing us to do things that in the past we could not do.”
Post a Comment
You must be logged in to post a comment.