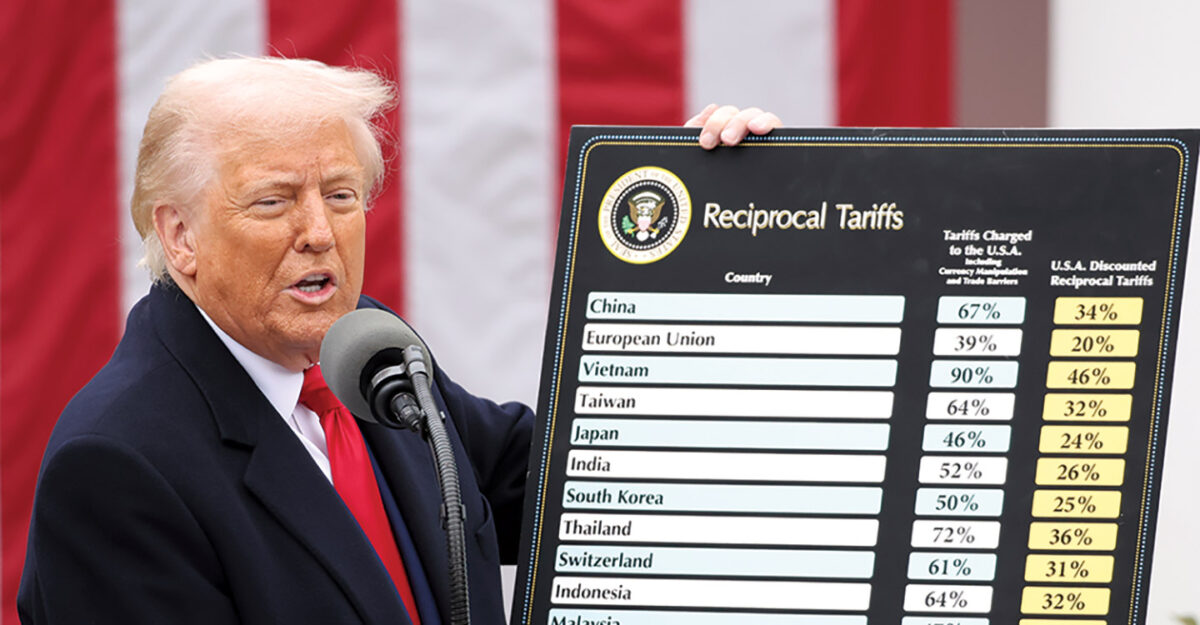
ENR 2025 Top Owners Sourcebook: Tariff ‘Golden Age’ Stuns Construction Market
✕
Overall, the value of construction-in-progress (CIP) for ENR’s Top 425 Owners rose 9.3% to $595.84 billion from 2023 to 2024. Part of that rise could be attributed to more moderately sized projects coming online, according to owners, as megaprojects tied to federal infrastructure packages mature and free up labor resources.
Total CIP for firms ranked in the top 100 rose 9.3% last year when compared to the equivalently ranked firms the year before. Total CIP for the bottom 100 firms also rose 24.2% during that same time frame. Moreover, median firm CIP rose 16.4% between last year, after decreasing between 2022 and 2023.
However, in a March labor data report, Associated Builders and Contractors (ABC) chief economist Anirban Basu pointed to an incremental tide change that could signal larger changes ahead. The construction unemployment rate decreased to 5.4% in March and is unchanged from one year ago, he reported.
“At first glance, this is a perfectly fine jobs report for the construction industry,” added Basu. However, he said “the details give cause for concern.”
Employment increased 1.8% since March 2024, the slowest year-over-year growth in four years, according to ABC’s analysis of data released by the U.S. Bureau of Labor Statistics.
“With downward revisions to the January and February numbers, the industry added just 8,000 jobs per month during the first quarter of 2025,” said Basu. And as employment slows, Trump’s tariffs could be the X factor that stalls construction in progress gains, says Basu.
“What amounts to the largest tax hike since 1968 will reduce construction activity due to rising input costs, shaken business confidence and potentially higher-for-longer interest rates,” he explains. “While contractors were sanguine about the [economic] outlook as of last month, according to ABC’s Construction Confidence Index, industry expectations are likely to worsen in the coming months.”
Market Focus: Environment | By Corinne Grinapol
Austin’s $1B Wastewater Treatment Fix
Photo courtesy of Austin Water
Work will start this summer on the $1-billion expansion and upgrade of the Walnut Creek Wastewater Treatment Plant in Austin, Texas. The project, being built using construction-management-at- risk delivery, will add 25 million gallons per day of treatment capacity to its current 75 million mgd to support the city’s growing population. It has roughly tripled since the plant opened in 1977 with an 18-mgd capacity, then supporting a population of 321,900.
The plant (see above) was expanded in 1987, 1990 and 2005 to its current capacity, but “demands have outpaced capacity,” Charles Celauro, Austin Water assistant director of engineering services, told press. “In 2024, several times we actually exceeded 90% of the capacity of the plant.”
“Demands have outpaced capacity. In 2024, several times, we actually exceeded 90% of the [wastewater treatment] capacity of the plant”
Charles Celauro, Assistant Director of Engineering Services, Austin Water
Roughly $440 million of the upgrade will go specifically to capacity expansion, including addition of nutrient removal and ultraviolet light disinfection. Another $220 million will fund conversion of the plant’s existing treatment process to nutrient removal and UV disinfection in a shift from chlorine, making it safer for residents and workers, according to public utility Austin Water. “With these investments, every part of the treatment process will be enhanced and upgraded,” said Shay Ralls Roalson, Austin Water director, in a press release last year announcing city council approval of contracts for the project. New influent and outfall pipes will also be installed.
AECOM is prime consultant on the project with a scope of work that includes process, mechanical, civil, electrical and structural engineering. In addition to designing both the upgrade and expansion, the firm also is incorporating resilience features into the plant in the form of a flood wall and wet weather treatment with added 100-mgd cloth filters. The flood wall will be built to resist a 100-year-flood event, based on a recent National Oceanic and Atmospheric Administration rainfall study. In addition to indicating an increase in significant rainfall events for the area, the analysis shows that the plant is in the 100-year floodplain.
Other work includes renewal projects totaling about $270 million to rehabilitate the primary and flow equalization basin and headworks building and to replace and upgrade the influent lift station.
The plant will be in operation throughout construction, which is anticipated to complete in 2031.
Prepping for Policy Change
In a panel discussion organized by the Construction Owners Association of America, several capital project managers representing educational institutions told ENR that they had expected the Trump administration to implement tariffs. Although it is “too soon to tell” how any tariffs will impact their capital projects, their ability to move forward through challenges is often tied to the needs of students and faculty and the availability of funding.
“The university is very dynamic to say the least. Our programs are rapidly changing. We do a lot of renovations based on what faculty members are doing,” says Mike Kelley, associate director of construction at Carnegie Mellon University.
Kelley adds that the one instance he could think of in which a capital project needed to be revisited was due to program development.
Drew Furry, project executive at Purdue University, agrees: “I would say that we’re definitely keeping an eye on some of those things, and the way our market will respond—whether it’s immigration or tariffs.” He adds, “If the market starts responding in a certain way over the next few months, we may react differently. But I don’t think it’s a key driver to our project delivery.”
Virginia Tech capital project manager Paul O’Keef says the university undergoes intensive planning for projects in advance. As a result, any adjustments to market conditions must also be completed according to intensive planning standards.
“It’s like turning a battleship” he says. “It’s very difficult for us to respond in the moment. Often when the market shifts, it’s something we have to bear.”
He cites the COVID-19 pandemic as an example of a market disruptor that came along so quickly that the university simply had to work through it.
“If the tariffs come in such a way that truly blows up our budgets, especially when something has already begun, we won’t know that until it happens,” says O’Keef. “Oftentimes, the state wants us to have concrete numbers before they would be willing to provide us with additional funding.”
Vince Yauger, assistant vice president for engineering, construction & planning at the University of Texas at Dallas, adds that the university also mostly takes a wait-and-see approach to market changes.
“The interesting thing is, we did such a hard left to a hard right shift that the ripple effects are going to be far reaching,” says Yauger, comparing tariffs to the previous administration’s attempts to jumpstart the economy with the Infrastructure Investment and Jobs Act after the COVID-19 slowdown. Yauger predicts tariffs will have the same affect on the market in terms of cost escalation and inflation.
“You can argue that with a stronger leader in the White House that we may have less volatility in the market,” says Yauger. “You could also argue the opposite.”
Crews work around the foundations and structural frame of BlueOval SK Battery Park facility No. 1, a joint venture between Ford Motor Co. and SK Innovation.
Photo courtesy of Gray Construction
Doubling Down on the ‘Golden Age’
In addition to up to 50% in “reciprocal tariffs”—which is actually calculated off of the U.S. trade deficit with a country rather than tariffs imposed on the U.S. by those countries—on imports from up to 90 countries, including China and the European Union, President Trump announced a 10% baseline tariff on all U.S. imports that went into effect April 5.
The U.S. stock market had its “largest two-day loss on record,” in the couple days after Trump’s tariff announcement, wiping out 5 trillion in value as all three U.S. stock markets closed with their worst days since the COVID-19 pandemic, reported MarketWatch.
Despite Wall Street leaders calling for him to rethink his tariff policy and consider how it will bruise the economy, Trump urged Americans to “hang tough” in an April 5 Truth Social post. The next day, during an interview on Air Force One as he returned from Mar-a-Lago, he characterized the tariffs as “medicine” needed to improve the United States’ trade deals.
“I don’t want anything to go down, but sometimes you have to take medicine to fix something,” he told a press pool on the plane. “What’s going to happen to the markets, I can’t tell you. But our country is much stronger.”
Echoing Trump’s sentiments, White House press secretary Karoline Leavitt called the tariffs the “golden rule” for the “Golden Age” of America, a phrasing Trump has pushed behind his second-term initiative to revive American manufacturing (manufacturing jobs increased during the Biden administration).
In a CNN interview, Leavitt said that Americans “can expect price stability. They can expect to buy American,” adding, “It’s a patriotic thing to do, and, most importantly, they can expect their wages to go up.”
However, given the impermanence of tariffs, Basu counters that business owners most likely will find that the tariffs don’t outweigh the cost risks of moving their operations to American soil.
“About 50% of U.S. imports are inputs to manufacturing. Massive taxes on manufacturing inputs are not an incentive to build a factory here,” says Basu.
However, during a Q1 construction economics update, Basu did commend the reciprocal tariff idea as a mechanism that could lower tariffs on U.S. exports.
“As an economist, we generally don’t love tariffs, but I think that reciprocal tariffs, at least conceptually, are quite brilliant,” said Basu—that is, if they work. Basu predicts that the “short-term pain” Americans will feel is the slide into a recession—if it’s not already here.
“Because we don’t have Q1 data, it is conceivable that recession has already begun in America,” says Basu. He says the market “was set to slow even before all this talk about tariffs.”
Market Focus: Power | By Debra K. Rubin
Ohio Data Centers Are Hungry for Gas

Image courtesy of Williams Cos.
Three large gas-fired power plants are set to be built in Licking County, Ohio, which is becoming a central U.S. data center hub. One is the PowerConneX New Albany Energy Center, a 120-GW facility to be built by Herndon, Va., developer EdgeConneX in a co-located data center. The Socrates North and South power generation facilities will be built by Will-Power, a unit of Tulsa, Okla.-based gas pipeline company Williams Cos.
EdgeConneX did not disclose the cost of its proposed project, but said it would be located near where Intel is developing an estimated $28-billion computer-chip manufacturing campus. The company expects construction to start later this year, with commercial operation in 2026. No contractor was disclosed. The project must be approved by the Ohio Power Siting Board, which will consider environmental impacts and community concerns. The data center would be its first in Ohio, the firm said, noting at least 28 data centers in North America.
Hyperscalers “don’t really want to have to go to the … power generator to build the generation and then to manage that.”
Alan Armstrong, President and CEO, Williams Cos. Tulsa, Okla.
The Socrates projects are separate gas-fired power plants, (see red outlined areas above) each with 200 MW of generation and pipeline connection to the Marcellus shale gas supply. Williams is investing $1.6 billion in the project, it said in a federal filing. Firm president and CEO Alan Armstrong says that with speed to market critical, hyperscalers seek “behind-the-meter” power generation that is not dependent on lengthy grid connection.
“These companies don’t really want to have to go to the gas company to buy their supply and to the power generator to build the generation and then to manage that,” he said in a Bloomberg TV interview. “They want somebody to show up with the power and provide the gas supply to provide that power, something that Williams is really well positioned to do.” The Socrates plans have a target start-up in the second half of 2026.
Developer Vantage Data Centers last year announced a $2-billion data center campus in New Albany, with Turner Construction Co. as general contractor, ENR has reported. Microsoft Corp. said last year it plans to spend $1 billion building three data centers in the county, gaining a 15-year local property tax abatement for its 197-acre site. Officials of utility AEP Ohio have been working with state officials to determine a rate structure for energy use from the growing data center industry.
Tariff Tit-for-Tat
Even if the tariffs are halted immediately, JPMorgan chief economist Bruce Kasman agreed with Basu that a recession is imminent, in a April 3 research note titled There Will Be Blood.
“Disruptive U.S. policies have been recognized as the biggest risk to the global outlook all year,” wrote Kasman. “The effect of this tax hike is likely to be magnified—through retaliation, a slide in U.S. business sentiment, and supply chain disruptions.”
The next day, Kasman’s prediction came to fruition as China announced that it would impose a 34% tariff on imports of all U.S. products beginning April 10.
In a statement, China’s State Council Tariff Commission said that it has filed a lawsuit with the World Trade Organization over the Trump administration’s tariffs policy, and it will subject 27 firms to trade sanctions or export controls, among other restrictions.
The Tariff Commission’s retaliatory tariff rate matches the tariff rate levied by the Trump administration. Scaling up the retaliation, Trump threatened to impose an additional 50% tariff on imports from China if the country does not reverse its retaliatory import fee.
In a Truth Social post on April 7, Trump criticized the country’s actions as “wrong” after Treasury Secretary Scott Bessent warned that retaliation would escalate tariffs into a trade war.
“CHINA PLAYED IT WRONG, THEY PANICKED — THE ONE THING THEY CANNOT AFFORD TO DO!” Trump added in a Truth Social post.
In yet another post, Trump wrote: “The United States has a chance to do something that should have been done DECADES AGO. Don’t be Weak! Don’t be Stupid! Don’t be a PANICAN (A new party based on Weak and Stupid people!). Be Strong, Courageous, and Patient, and GREATNESS will be the result!”
Tariff Ripple Effects
According to a White House release, key construction materials such as steel, aluminum, lumber and copper will be exempted from these additional tariffs.
At the design level, American Institute of Architects chief economist Kermit Baker says firms and owners should still expect increased material costs in the short-term. According to Baker, the increases will put further pressure on already declining architectural billings as developers and clients reassess budgets.
“Over the long term, it’s still early to predict how much of an impact, but persistent cost inflation and uncertainty could slow project pipelines, leading to continued volatility in architectural billings,” says Baker. He adds that it is still premature to comprehensively estimate the negative effect the tariffs and trade policies will have on the overall market.
“It will depend a lot on the extent of international blowback, as well as the domestic response,” says Baker.
But for many owners, it’s uncertainty they’ve navigated before.
Gloria Samuel, a senior vice president at Fifth Third Bank, says she’s already been informed that she will see tariffs on mechanical equipment. The hike in pricing comes just as she was starting to see a flattening from COVID-19-era volatility.
“I feel like it would be very thoughtful to pay attention to how we acquire material,” says Samuel, adding that it is difficult for the publicly traded company to change course once it communicates its plans to the market.
“If there is an opportunity for us to do an early purchasing, we consider that,” says Samuel.
Baker predicts that the tariffs will force construction companies based in the United States to look for alternative suppliers for a range of building materials. As a result, “architecture firms will need to better understand how these changes will affect the cost and availability of these materials,” he says, adding that design firms will also “need to supply alternative designs to accommodate the realities of materials costs and availability.”
Overall, Baker says design activity at U.S. architecture firms has been weak since the fourth quarter of 2022. “High interest rates and declining commercial property values have been the principal sources of this weakness,” he explains.
the tariffs will shift concerns, adds Baker. Now that Trump has officially implemented his tariff plan into practice, Baker says owners can expect to see direct effects to construction costs should the tariffs remain in place.
“Over $2 trillion was spent on construction projects in the U.S. last year. The cost of materials and products used in these projects generally accounts for around 50 percent to 60 percent of total construction costs, so likely amounted to well over a trillion dollars last year,” says Baker. “While most of the construction inputs are produced domestically, in this age of globalization, many materials and components are imported and will see higher prices.”
Market Focus: Oil & Gas | By Debra K. Rubin
Delfin US Floating LNG Export Site Gains
Photo courtesy of Delfin
Delfin LNG LLC has gained two key federal approvals in recent weeks to move forward in the construction of what it says will be America’s first newly built deepwater port and floating export terminal facility for liquefied natural gas.
Set to be built between 37.4 and 40.8 nautical miles offshore of Cameron Parish, La., the facility will be able to produce up to 13.2 million tons per year of LNG, according to the developer. Its estimated cost ranges to $7 billion. Delfin, majority-owned by Fairwood Peninsula, Talisman Global Alternative Master and Talisman Global Capital Master, says it expects a final investment decision later this year.
South Korea-based Samsung Heavy Industries has been named engineering, procurement, construction and integration contractor, with Black & Veatch, Overland Park, Kan., providing design and technology for the modular project of four floating LNG units. Delfin has sought to build it for more than a decade, buying an existing 30-mile, 42-in. pipeline in 2014 to deliver natural gas to the floating site.
U.S. LNG firm Delfin’s 15-year+ deal with German company SEFE “ensures security of supply for customers in europe and around the world.”
Frédéric Barnaud, Chief Commercial Officer, Sefe
The Delfin project gained a Federal Energy Regulatory Commission green light in 2022 to start construction, but two approvals remained. U.S. Energy Secretary Chris Wright, OK’d in March a permit extension to mid-2029 for facility LNG export to countries without a U.S. free trade agreement, comprising a major global market sector. The Biden administration had paused the permit, as it did for other facilities. Since January, Wright has approved a similar extension for the Golden Pass LNG site in Texas owned by QatarEnergy and ExxonMobil. It also conditionally OK’d two other Louisiana projects, Commonwealth LNG, owned by Kimmeridge Texas Gas LLC; and Venture Global’s CP2 project. Said to cost $28 billion, the latter has no final investment decision.
Announcing the Delfin permit at the energy sector CERAWeek by S&P Global event in Houston, Wright said he was “thrilled to sign this order to help another U.S. LNG project advance.” As part of the Trump administration “energy dominance” agenda, DOE rescinded a Biden policy that required LNG projects to export within seven years of approval, which it says allows more time to finish work.
U.S. Transportation Dept.’s Maritime Administration also issued the Delfin project developer a license to own, build, operate and eventually decommission the deepwater port facility, which the agency denied last year, stating that the export site’s design, finance and operating plans had changed too much since a recommended approval in 2017.
Delfin and German firm SEFE inked a March 25 pact for 1.5 million tons per year of LNG for at least 15 years that “ensures security of supply for customers in Europe and around the world,” said Frédéric Barnaud, SEFE chief commercial officer. That follows other Delfin deals since 2022.
But market observers still see LNG project risks from environmental legal challenges. “Litigation is the real problem, and that can only really be tackled by Congress,” Thomas L. Sharp, director of permitting intelligence for energy research consultant Arbo, told sector publication Natural Gas Intelligence last month.
Economic Déjà vu
In March, Trump imposed a 25% tariff on all steel and aluminum imported into the United States, a move that many manufacturers recalled from his first term as he made a push for American steelmakers. CNN reported that Canada and the European Union retaliated with tariffs on a broad range of U.S. exports within hours.
Alcoa, one of America’s largest aluminum makers, warned that the tariffs could cost the company 20,000 jobs. President and CEO William (Bill) F. Oplinger explained that a significant part of its aluminum production is located in Canada, where energy efficiency lowers its production costs. Data from the Anderson Economic Group estimated that the tariffs could tack on $250-$2,500 in additional costs for all car purchases.
Data and analytics firm Wood Mackenzie estimated that the effects of the steel and reciprocal tariffs will also ripple across the oil and gas industry in the form of cost pressure. On April 6, the New York Times reported that oil prices briefly dipped below $60 a barrel, its lowest in nearly four years.
During his first administration, Trump made exemptions for exports of oil country tubular goods (OCTG), says the firm. However, Trump has suggested that such exemptions would be more difficult to come by this time around.
The U.S. typically imports about 40%-50% of its OCTG, says Nathan Nemeth, Wood Mackenzie’s principal analyst for global unconventional plays. Tighter tariff rules with fewer exemptions would “likely have an impact on prices,” he says.
Additionally, “OCTGs represent about 8.5% of drilling and completion costs for onshore wells in the U.S. lower 48 states. So if prices rose by 25%, to reflect the tariff impact in full, about 2.1% would be added to well costs,” says Nemeth. He adds that OCTG prices roughly doubled during the pandemic. Although Nemeth estimates that the impact of tariffs could be much smaller than pandemic-level inflation, “it would create an extra cost pressure on the industry at a time when companies were already planning for cautious growth in production,” he says.
Investing in the Future
As much as tariffs call attention to construction costs, they don’t erase existing industry challenges such as skilled labor shortages, supply change disruptions and finding dependable contracting partners, owners’ representatives told ENR. “Labor has continued to be a challenge for our industry for quite some time,” says Samuel.
Yauger adds that his team anticipates labor challenges deepening as Trump ramps up investments in data center building and infrastructure to foster oil and gas drilling.
In Indiana, Furry says that megaprojects are still having an impact on the availability of labor and material resources, but some contractors are choosing not to bid for such projects due to their time commitments.
“Some companies are making a decision not to pursue megaprojects because [they] don’t want to commit 70% of staffing and bandwidth to one project,” says Furry.
Amid material price volatility and increased risks, the capital project managers say they expect to see owners begin prioritizing people over prices, moving away from traditional design-bid-build models to more collaborative alternative delivery models.
“I think anyone who has been in this business for a while realizes that no single builder is the same as any other builder,” says Virginia Tech’s O’Keef.
He adds, “We may get a project that may ultimately get delivered, but the process of that delivery is going to be incredibly different depending upon who we work with.”
Samuel adds, “As an industry, I think we have some work to do. We definitely need to be innovative in our thinking in how we approach our construction efforts.”
Stephen T. Ayers, interim executive vice president and CEO of the American Institute of Architects, pledged that the institute would continue to “advocate for the repeal of these trade barriers with the [current] administration and Congress.”
“In the face of potential increased construction costs and slowing growth, AIA will continue to advocate for policies that support economic growth and a strong construction sector,” says Ayers.
The institute is also providing resources to help members run their businesses effectively and navigate these changes, such as its AIA Business Academy, says Ayers.
He adds, “These tariffs, if they remain in place, will negatively impact our 100,000 members in the U.S. and around the world by artificially inflating prices while damaging the reputation of American professionals as good global business partners.”
Post a Comment
You must be logged in to post a comment.