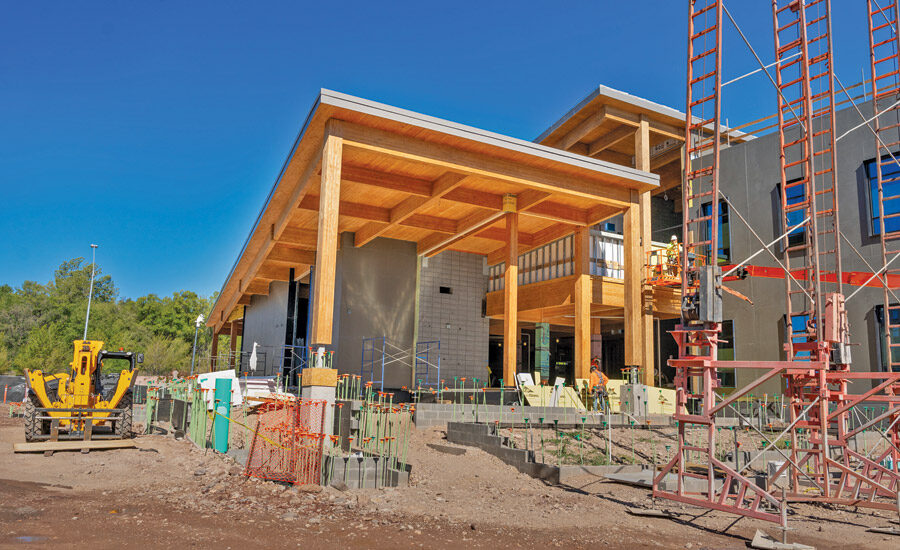
Bus Facility Brings Mass Timber to Northern Arizona
Transit riders in Flagstaff, Ariz., looking for a central hub have been greeted by a “temporary” facility—essentially a glorified parking lot—for more than a dozen years. But a new project wrapping up in the next couple of months will provide a dramatic upgrade.
The $25.5-million first phase of the Mountain Line Downtown Connection Center nestles into an extremely tight footprint surrounded on three sides by a busy railroad line, the main roadway to downtown Flagstaff and active bus terminals. The two-story, 20,938-sq-ft operations center brings mass timber construction techniques to Northern Arizona for the first time, and it is only the second such building in the state.
The project highlights the warm colors of mass timber, CMU masonry and exterior stone cladding.
Photo courtesy Emily Gerdes/Loven Contracting
“We wanted to build a great welcoming center to support our riders and to showcase transit in our community,” says Anne Dunno, capital development manager for Mountain Line. “The focus of Phase 1 is public space: It’s point of sale, it’s community center, public restrooms and really enhancing the ties to transit.” Phase 1 also includes 11 bus bays.
The building didn’t start out as a CLT structure. The initial design, produced by AECOM for master planning and to get the project through federal grant applications, specified a steel structure with ‘wood-look’ panels to meet Flagstaff’s stringent high-country architectural standards, says Kate Diamond, design director for HDR, the building’s architect. But Diamond, who “if cut would bleed green,” colleagues say, proposed using mass timber both for aesthetics and to meet sustainability goals for the net-zero energy use structure. “This was not just a decision relative to mass timber and reducing embodied carbon, but it is an overall integrated design approach,” she says. That said, using CLT dropped embodied energy costs by more than 30% compared with a traditional steel structure, according to HDR data.
Construction manager at-risk Loven Contracting hadn’t worked on a mass timber building before, but after visiting Arizona’s first such project—Mortenson’s offices in Tempe, a finalist two years ago for ENR Southwest’s Project of the Year—and pricing out the materials, labor and schedule, Loven saw that the cost difference was negligible.
At an elevation around 7,000 ft, Flagstaff winters can be severe. Average snowfall reaches 119 inches per season, but the city saw 163 inches during the project’s first winter.
Photo courtesy Emily Gerdes/Loven Contracting
“We were engaged early, even before we saw the 30% drawings,” says Jon Hansen, Loven president. “So we were really able to provide a lot of support in cost estimating as well as constructibility reviews.”
With mass timber being so new to Arizona, Loven has had to facilitate an extended planning process as well as educate local trade partners. To lend additional expertise, “we went out for a qualifications-based solicitation for the mass timber trade partner and selected Timberlab out of Oregon to partner with, bringing them in at 60% drawings, which really helped to finish the design.”
HDR, Loven and Timberlab also engaged with the city of Flagstaff early “before we’re sitting there with a set of plans needing a building permit” and discussed “what was going to be included in the plans, what some of the industry standards are and what the city would like to see to help them feel comfortable and be able to issue a permit for a mass timber building,” Hansen says.
“We worked with the city to get a foundations-only permit in place prior to our mass grading being completed”
—Kevin Cody, Sr. Superintendent, Loven Contracting
With much of the prep work done, site demolition began in March 2023, which came with its own set of challenges. In addition to being hemmed in on all sides by transportation lines under different jurisdictions—a BNSF railroad to the north with 125 freight trains running every day, ADOT’s roadway to the west, a Flagstaff street to the south with a dozen Mountain Line busses arriving and departing every half hour and a future large-scale Army Corps of Engineers-led flood control project, Rio de Flag, to the east—construction crews also had to place underground a high-voltage power line feeding downtown Flagstaff that runs right through the site, says Kevin Cody, a Loven senior superintendent.
The site also sits within a 100-year floodplain, which required mitigation. After studying various technologies, “we found out that if we just went up 6 more inches, we’d be at the correct height that we would need to be to not have any flood protection,” says Jarod Bogenrief, project architect with HDR. The project adheres to universal design, and access ramps, landscaping features and stairs are integrated into the entry plaza without the need for guardrails except in a few discreet spots.
The Build America, Buy America project featured materials manufactured in the U.S., and many of the trade partners hailed from the region.
Photo courtesy Emily Gerdes/Loven Contracting
Because the tiered site walls serve as both retaining walls and ramp walls, phasing of sitework had to be meticulously planned. “We worked with the city to get a foundations-only permit in place prior to our mass grading being completed,” Cody says. In addition, a 12-ft-deep sewer line had to be completed early on before the building’s footings were placed, he adds.
The project began going vertical in fall 2023 to get ahead of the winter season. Due to the fabrication timing for the mass timber, the project’s load-bearing masonry walls had to be built first, which also serve as the building’s shear walls. “That meant we had to get all of these walls up to full height, with tolerances that were plus/minus 3/16 in. from Timberlab and another 3/16 within the masonry tolerance,” says Kevin Bond, Loven senior project manager. “To combat that, we surveyed about every 4 feet to ensure that we weren’t waving in and out of our walls.”
The nearly completed central stairway highlights the exposed structural elements of CMU and mass timber. Light will penetrate through Solatubes in the ceiling (not yet installed in the circular openings shown in this photo).
Photo courtesy Emily Gerdes/Loven Contracting
Diamond says “the polished CMU block wall and the quality of craft looking down that daylit corridor are as smooth as if we had specified marble.” He credits the overall commitment to craft by Loven and its trade partners, including masonry contractor G&G Masonry. “It’s the straightest and cleanest CMU work that I’ve seen in 40-plus years as an architect.”
With masonry completed, the team faced their next challenge. “Once we pulled the scaffolding down, we had no room to brace these walls because the mass timber had to fly-in in large beams, and the bracing would be in the way,” Bond says. “So we worked with our structural engineer to internally brace [the CMU walls] with additional rebar and engineering. A lot of these walls were freestanding and would sustain wind loads through the construction of the mass timber.”
As with most mass timber projects where the structural elements are exposed, MEP penetrations and voids had to be planned ahead at a level approaching prefabrication. Because the building programming includes office space, IT services, dispatch operations, a driver’s breakroom and a large training and community board room, designers worked with Mountain Line to nail down the interior layout and where power sources would be so penetrations and voids could be included during fabrication, says Jessica Levin, interior designer with HDR. “There really isn’t a lot of room for modifications in the field,” she adds.
“It’s the straightest and cleanest CMU work that I’ve seen in 40-plus years as an architect.”
—Kate Diamond, Design Director, HDR
One of the primary design goals was to celebrate the material, so there are only a few areas in hallways where drop ceilings and other strategies hide cabling and other systems.
“We wanted to honor the wood. Why are we doing mass timber if we’re not going to honor it?” Levin asks. The mass timber in the exposed ceilings and columns “really speaks to the area and also speaks to sustainability within Flagstaff.”
Structural engineer MBJ worked with Loven’s VDC team to preplan pipe routing through structural elements “and provided openings in the glulams for things like sprinkler piping to keep everything tucked up and high,” says Chad Sippel, structural engineer for MBJ. “There are also allowances for some small penetrations in the wood CLT panels that make up the floor system to give some flexibility to the contractor for placing things like small mechanical sleeves or electrical conduit penetrations.” Thanks to the planning, there were very few RFIs during construction.
Due to the lack of laydown space, the 30 or so semi truckloads of mass timber pieces had to be delivered in order of installation so they could be picked straight off the trailer, Hansen says.
Rendering shows the completed Phase 1 operations building with landscaping placed.
Image Courtesy Norris Design and HDR
Because of the tight site and locations of subsurface stormwater retention chambers that couldn’t handle heavy equipment resting above them, the team only had one zone on site in which to locate a crane with a long enough boom to reach the farthest diagonal pick. “Right when the trucks would arrive, the crane would pick the pieces right off the truck, all in sequential order,” Bond says. “There was a lift about every 15 minutes for about two weeks.” The results were “really accurate and efficient,” he adds.
Using mass timber saved on schedule length over steel, says Mike Loven, CEO of Loven Contracting. “And because the [Timberlab] workforce are not carpenters—they are people that are just trained to erect CLT—it’s a lot easier for them to get their talent pool, and at a more competitive rate.”
Since the structure also functions as the finished architecture, many of the connectors were routed into the ends of the beam and hidden within the wood itself. “It’s a very clean, functional structural connection that has testing and load values behind it,” Sippel says. “Similarly, the base plate elements on the wood columns are all hidden. However, they’re raised up off of the concrete to prevent any moisture infiltration.”
The connectors, wood, CMU and virtually all of the other manufactured building elements hail from the U.S. Having received federal funds, the project falls under the Build America, Buy America Act requirements.
Mass timber also comprises part of the exterior’s distinct look, though its location under an overhang helps to protect it from the elements.
Expected to begin construction sometime after 2028, Phase 2 will include a 13-bay bus plaza, public gathering space and charging facilities.
Image Courtesy Norris Design and HDR
Lowering Energy Use
Inspired by Northern Arizona’s robust sustainability culture and buoyed by the promise of lower operational costs, the team designed the project to achieve net-zero energy use. “Net-zero MEP systems support the building [and] include radiant heated and cooled floors, chilled beams, cold climate air source heat pumps and photovoltaic panels” that will supply about 80 kilowatts, says Brett McQuillan, senior mechanical engineer at Affiliated Engineers Inc. “The chilled beams in combination with the radiant floors let us minimize the amount of overhead distribution that was required in the building, which allowed us to expose more of the CLT mass timber structure.” Heating from below also boosts efficiency and reduces the overall volume needing to be heated, especially in Flagstaff’s cold winters.
Substantial completion for Phase 1 is scheduled for April 30, with final completion on June 13. While Phase 2—which will add a bus plaza with 13 bays, a civic space for community gatherings and electric bus charging stations—has already received funding “in today’s dollars,” construction is contingent on Flagstaff completing the Rio de Flag flood protection project, says Heather Dalmolin, CEO and general manager of Mountain Line.
McQuillan says the systems in place for Phase 1 go “hand in hand with the ultimate goal of this serving as a bus charging facility for Mountain Line, with a planned electrical demand of about 6 megawatts to support the full build-out of busses here, which would make it one of the largest point loads of power in Flagstaff for electricity.”
Post a Comment
You must be logged in to post a comment.