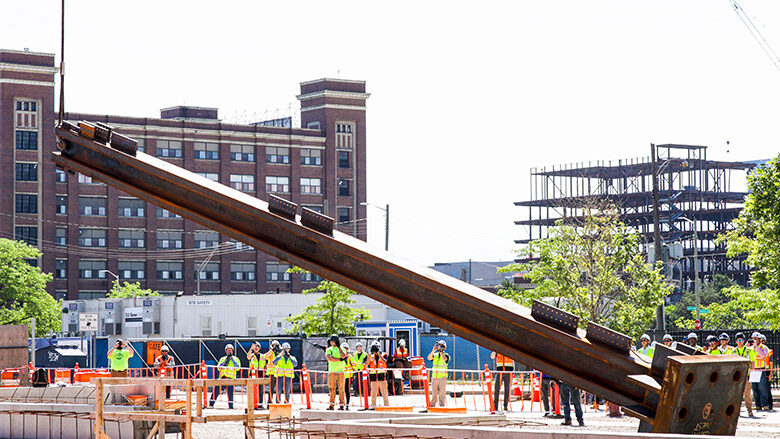
World-Record ArcelorMittal Steel Column Erected at Detroit Hospital
A project to build a 20-story hospital tower on the Henry Ford Health campus in Detroit has marked a worldwide first with placement of four W14x1000 steel columns installed at the bracing core at the base of the tower portion of the hospital.
The columns, each weighing 1,000 lbs per sq ft, were installed July 1 by crane at the hospital tower that will span 1.2 million sq ft, and which is the anchor of Destination: Grand, a $2.2-billion expansion of the hospital campus under construction by the Barton Malow-Turner-Dixon “tri-venture” joint venture construction team in partnership with Gayanga.
The columns were produced by Luxembourg-headquartered steel producer ArcelorMittal, the only company in the world currently producing columns of this jumbo size and shape.
“What makes this so special is the size of the column and the fact that it is a rolled shape,” says Joseph Dardis, head of construction presales at ArcelorMittal. “It’s very difficult to get that big with a solid, rolled shape. This was definitely a feat of research and development.”
Describing the process in non-technical terms, Dardis says “you’re taking a semi-liquid kind of [steel] form and smashing it between two giant pieces of machinery to get to its final state. A lot of the strength in the shape comes from the rolling process.”
Mark Braekevelt, senior director of steel operations and building trades for Barton Malow, says the W14x1000 column is “the ideal solution for supporting extreme vertical and lateral loads.”
He says the column is well-suited to a health care tower which has higher requirements for wind and seismic loads and needs to hold a lot of heavy healthcare technology and equipment.
“Before this shape was available, we’d have [used] more of a custom fabricated piece where we are putting multiple pieces together to form one column, which requires a lot more shop welding and a lot of fabrication,” Braekevelt
says. “It’s a lot more labor intensive to create a custom fabricated piece of steel.”
The W14by1000 columns—which Dardis says will be useful in a variety of other project types and in geographic areas, such as the earthquake-prone West Coast—did not save on weight but met other project needs.
“Henry Ford wanted bulk,” Dardis says. “They needed mass. So it didn’t necessarily save on weight, but it saved labor.”
Each column, made from 98% recycled scrap using ArcelorMittal’s electric arc furnace (EAF) technology, was less expensive than a custom-fabricated piece would have been, Dardis says.
In addition to being created in an EAF and not a blast furnace stoked by coal, the W14 by 1000 strategy saves on embodied carbon compared to a custom-created column, “because when you’re welding plates to a section, plates generally have a higher embodied carbon,” Dardis says.
The columns were approved in December 2023 by the American Society for Testing and Materials (ASTM). They are not yet included in the American Institute of Steel Construction’s Steel Construction Manual, which comes out every six years.
“It’s in our database,” says Chris Raebel, vice president of engineering and research for the American Institute of Steel Construction (AISC). “It’s available to use. It will be included in our next manual that comes out in 2028.”
Going Bigger
ArcelorMittal created the jumbo column shape to better address needs in the marketplace, especially as it looked at slackening demand in the commercial office space market.
“We really made an effort in the last few years to market a little differently with the absence of commercial office [demand],” Dardis says. “Health care was kind of a natural fit because a 10-story hospital might have the same column demands as a 30-story office just based on the intricacies of a health care project.”
Competition is another reason why ArcelorMittal created the W14x1000 column.
“We’ve always rolled the biggest shapes in the world, but other steel producers kind of catch up to us,” he says. “We keep going bigger and bigger.”
The columns were shipped from Luxembourg to Sippal Steel in Pittsburgh, Pa., which cut them to size and added connections before shipping them to Henry Ford.
The W14 x 1000 is lowered into place at Henry Ford Health in Detroit.
Photo courtesy of Barton Malow
ArcelorMittal believes there is demand for even larger steel columns.
“We know there is market for this and a market to go bigger [with the columns],” Dardis says. “Engineers and the steel community are just fascinated by how big this thing is.”
Destination Grand is also the first healthcare project in the world to incorporate A913 grade 80 sections, which ArcelorMittal says are the world’s strongest rolled steel shapes. Typically used in high-rise office towers, A913 is a high-strength, low-alloy structural steel produced using a quenching and self-tempering process. Grade 80 means it has a minimum yield strength of 80 kips per square inch. KSI is a unit of measurement for stress or pressure, defining the amount of force a material can withstand before deforming or breaking. One kip equals 1,000 lbs of pressure so 80 KSI steel is tested and confirmed to have an 80,000-lb yield. Its high yield also reduces overall steel tonnage and can reduce costs for projects.
Seeing the first W14x1000 columns installed at Henry Ford, which only took minutes to complete, was “amazing,” Dardis adds “The energy there was amazing. And there was a lot of excitement to see history being made.”
“This is another option in the toolbox of the designer so they can provide an efficient structure for the client,” Raebel says. “Is it always going to be the right answer? Maybe not. But it’s certainly a possibility and I am sure it will be considered for projects where they need extra beef in the columns.”
Braekevelt also sees great interest in the construction industry for this new shape.
“When construction-savvy people hear ‘W14by1000’ their ears perk up and their eyes light up,” he says.
Post a Comment
You must be logged in to post a comment.